When I purchased the Taig mill I immediately knew I would want an enclosure. Slinging chips everywhere is fine for a shop environment, but for a benchtop machine small enough to fit in a second bedroom an enclosure is a necessity. I set out to design an enclosure from 80/20 and settled on something very similar to what NYCCNC showed off in this Youtube video. While I had grand plans and fancy door designs, this simple, upward sliding door design proved to be a much more economical option. Anyone who has built a personal project from 80/20 can tell you the cost of the project will surprise you!
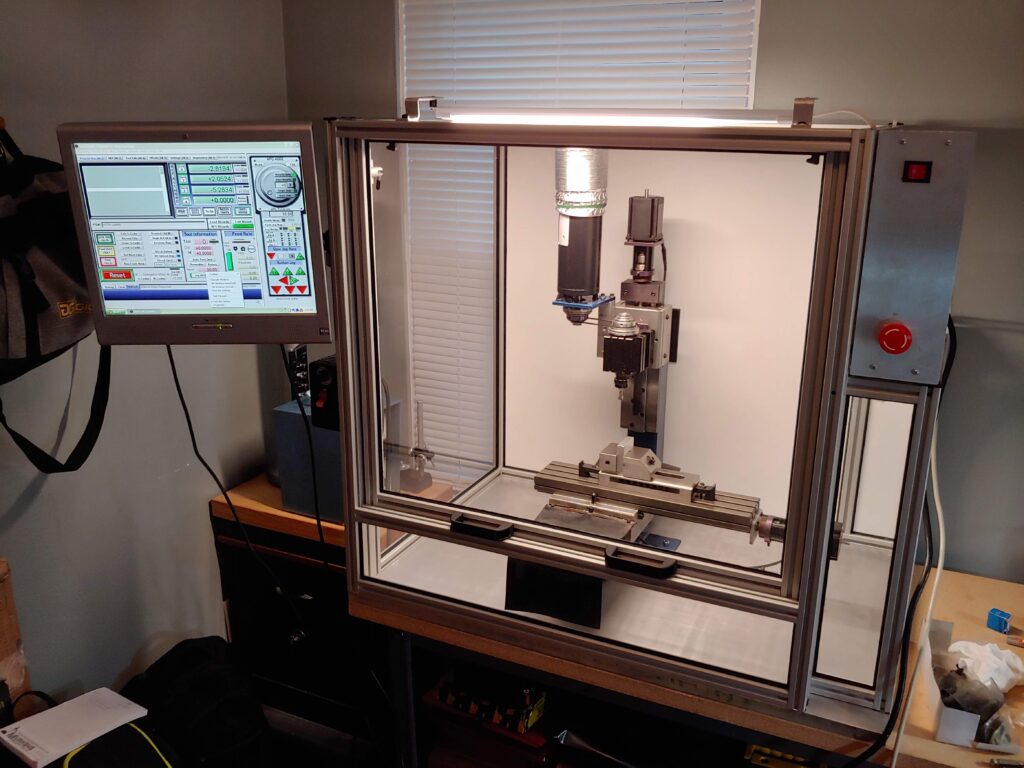
The final enclosure design features the aforementioned vertical sliding door that rides on a pair of UHMW rails affixed to the frame. Thanks to the modular nature of 80/20, it was easy to mount the mill control box, computer monitor, spindle control box, overhead lighting, and a neat little tool rack with only a few handmade aluminum brackets. I ordered all of the 80/20 without any machining and drilled access holes myself to save a few bucks. I purchased blank panels from 80/20 cut to size, and a co-worker was kind enough to let me use their router to make cutouts for the enclosure fan and vent on the top. There’s also a square cutout in the rear panel where I mounted an outlet cover with a brush style cable passthrough for the motor control and spindle power cables.
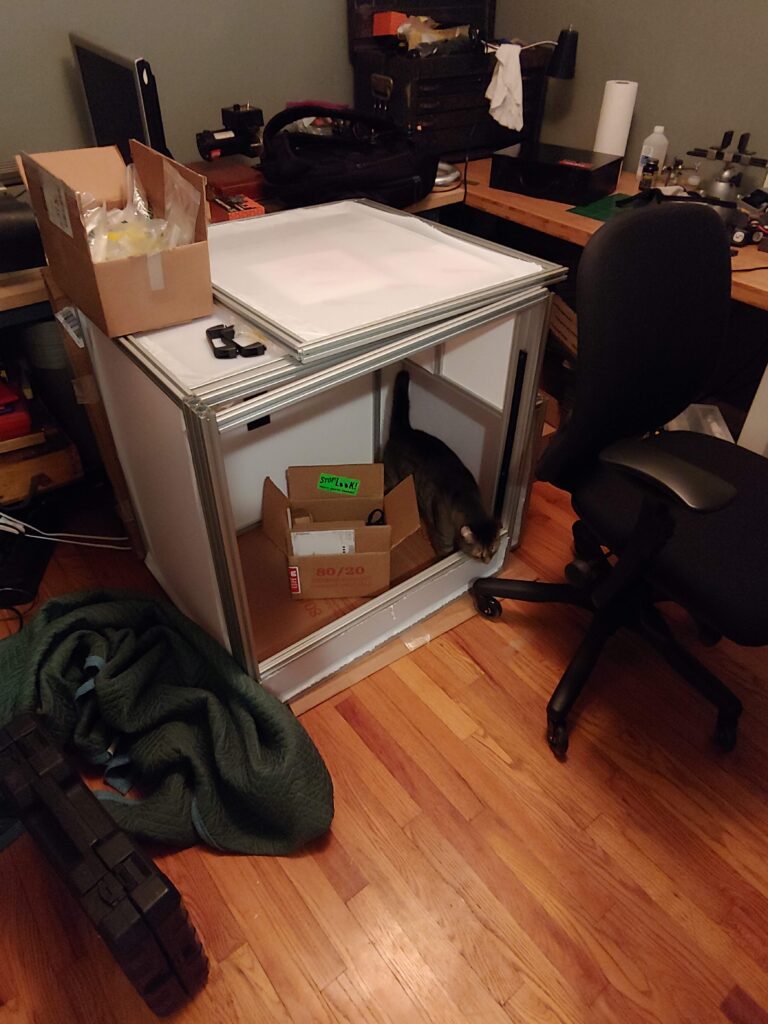
Assembling the frame in my small second bedroom turned out to be quite the challenge, but after only having to take it back apart half a dozen times I eventually got everything together. To light the enclosure I used an under-cabinet light outside the enclosure which is amazingly bright for the cost. For a baseplate I glued an 1/8″ thick piece of aluminum plate to a 3/4″ thick piece of MDF. I despise painted steel baseplates for this application because over time the paint chips off and they look awful. The aluminum won’t need a coating or paint to prevent rust and is easy to clean. I scuffed the surface of the aluminum with sandpaper to reduce glare from the overhead light, and caulked all around where the enclosure meets the base plate.
So far the enclosure has done an excellent job of keeping chips off of my floor and also cuts down on the noise from mill. The only thing I would change if I did it again would probably be using a piece of hardwood for the base instead of MDF, as the MDF had a tendency to split when attaching the enclosure to the base. While this project was expensive and not nearly as easy as I had imagined, having the ability to use the mill indoors is well worth the trouble!
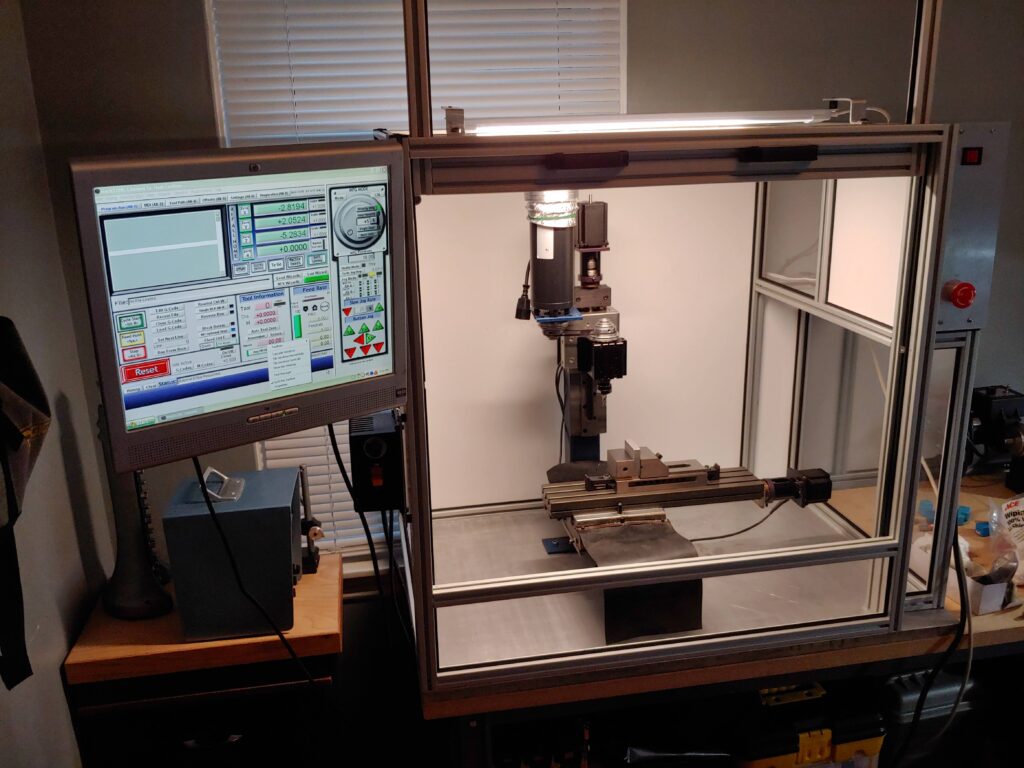
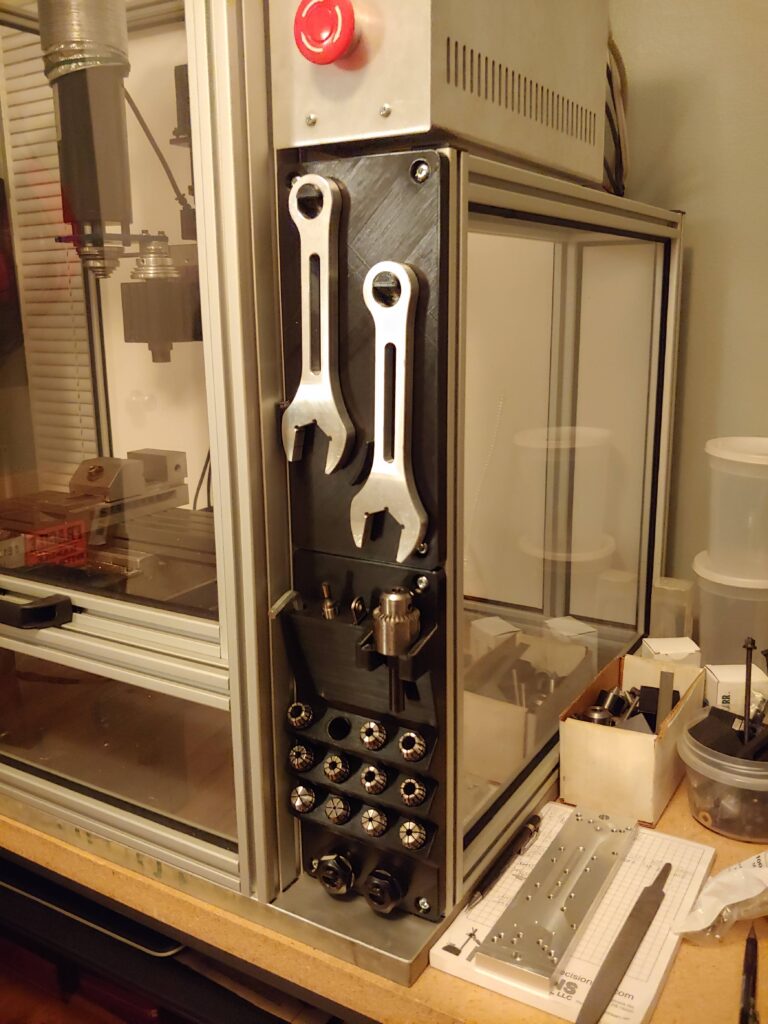
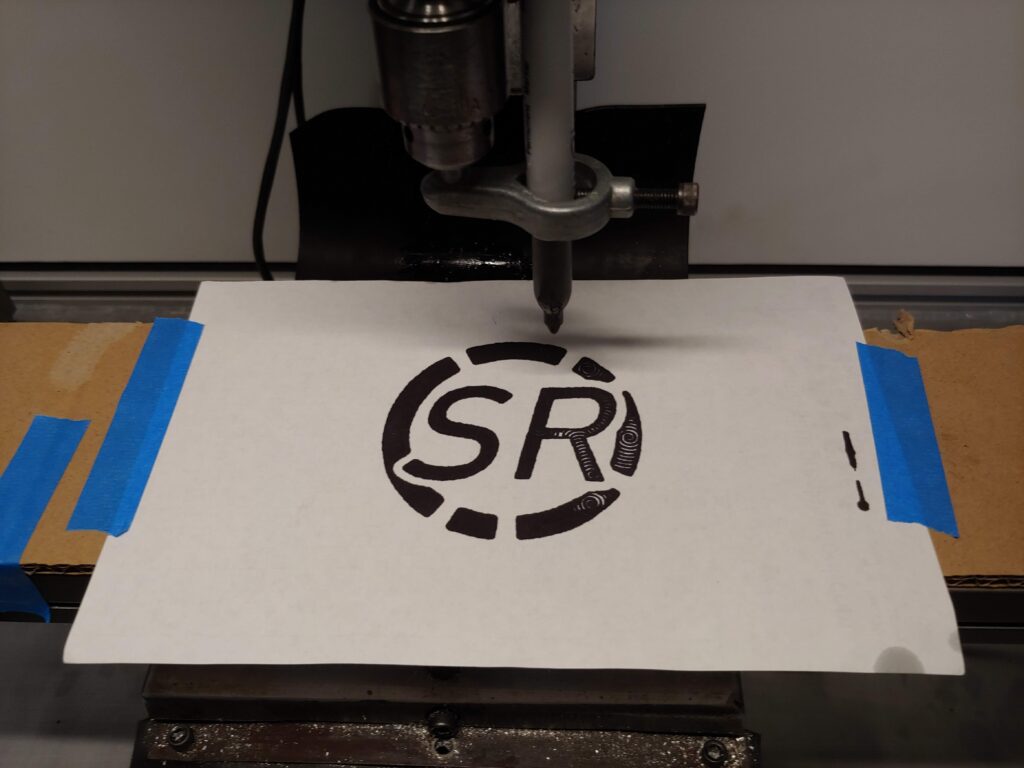
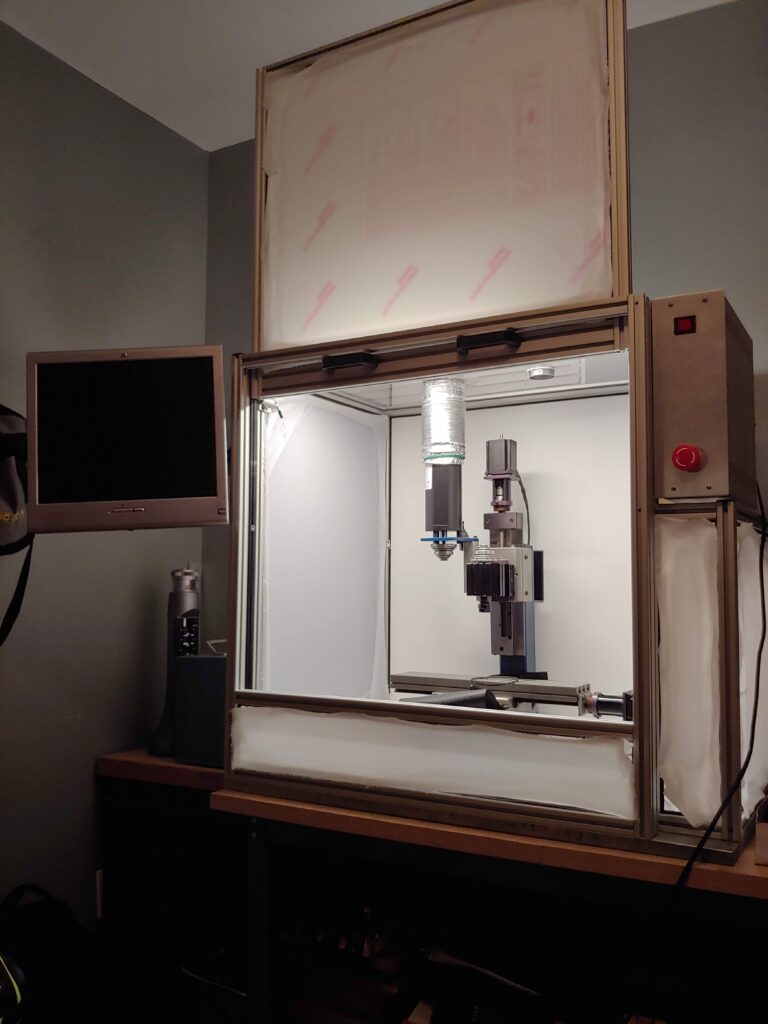
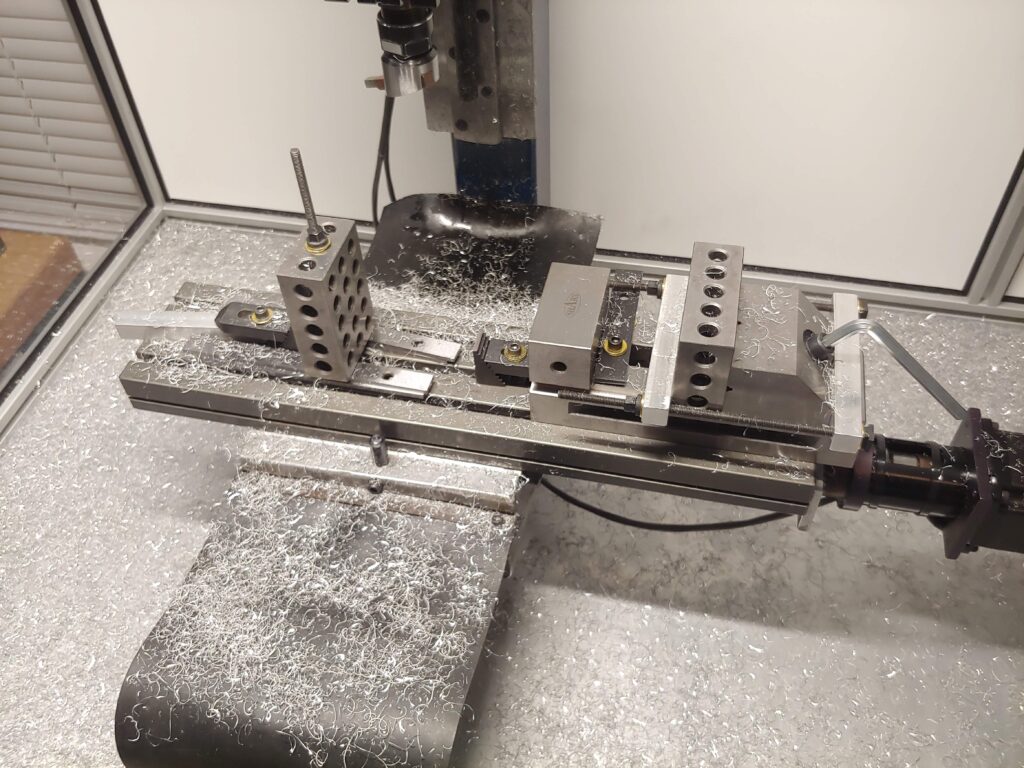
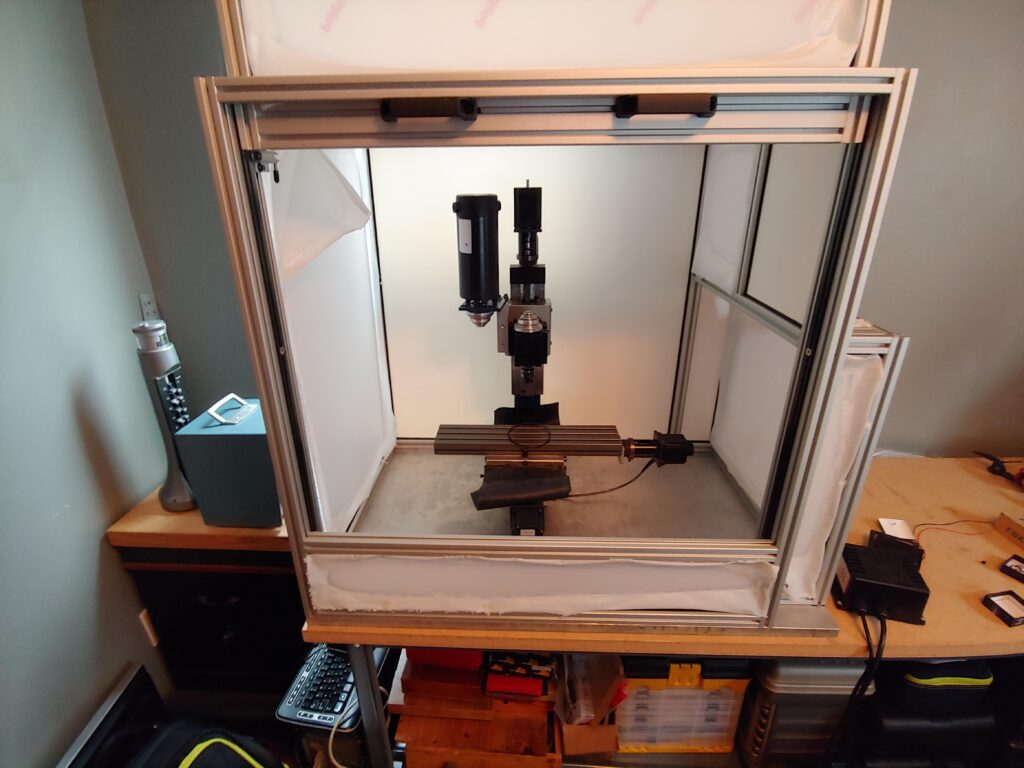