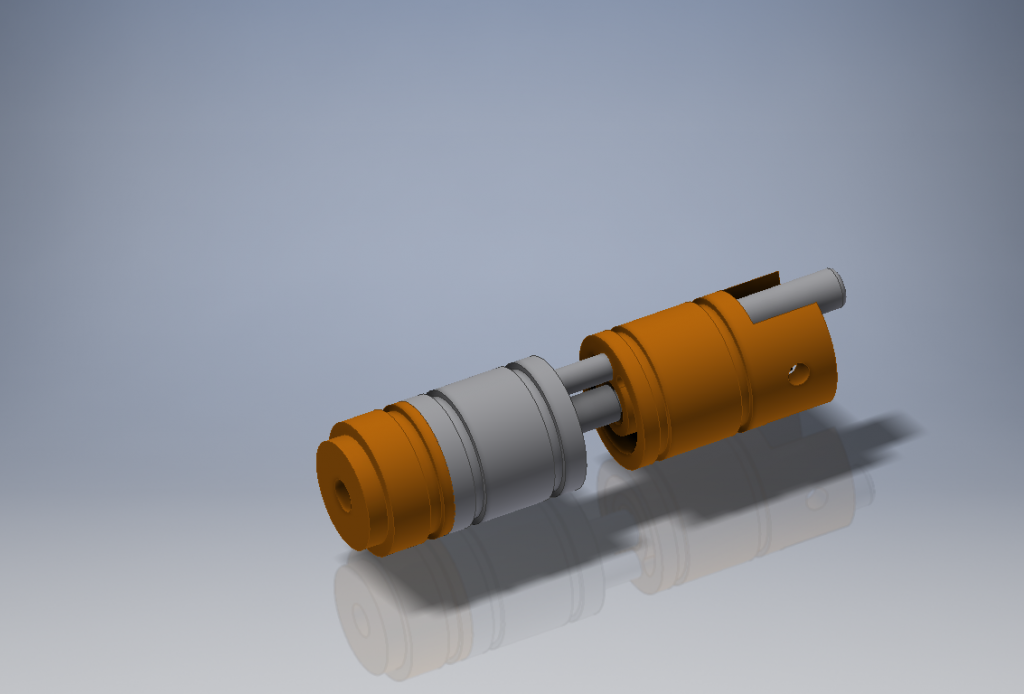
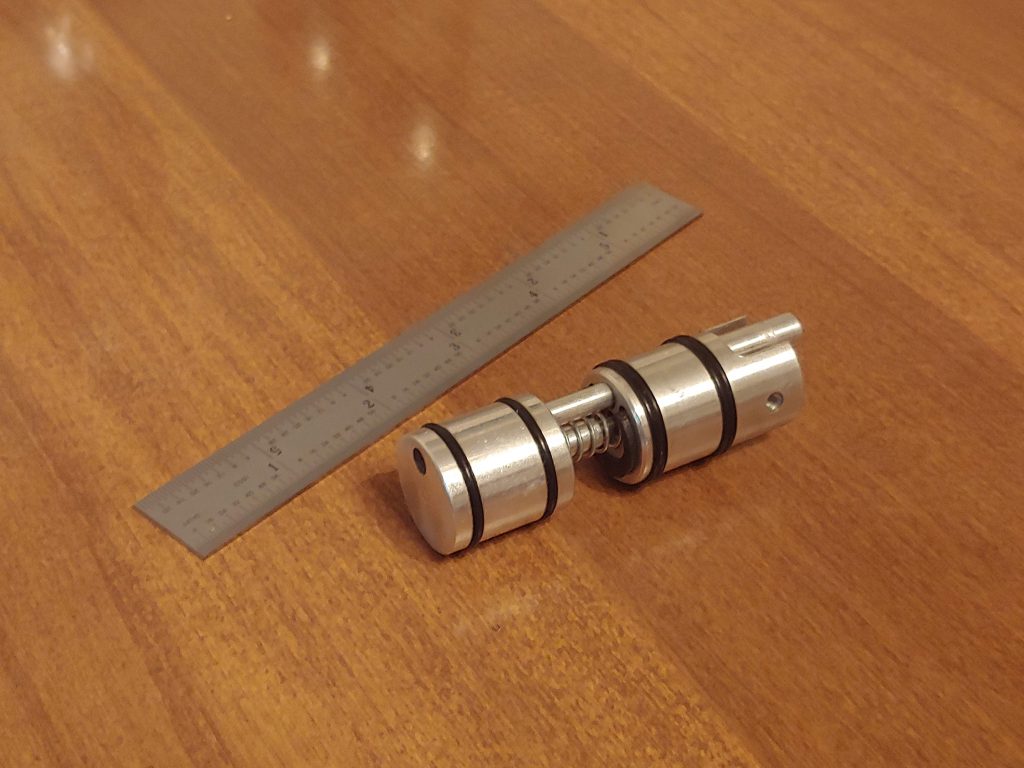
Early in my high school career I had an interest in small pneumatic air guns for target practice. The mechanisms they used to load and fire a projectile were extremely interesting to me, as many of them used a complex gear system with a spring-loaded piston to allow for a semi-automatic firing mode. At the time semi-automatic pneumatic designs were beginning to be developed, and one open source design was available. I found the simplicity of the design fascinating, but it was not compatible with the cheap, low quality air gun I had at the time. Having just been introduced to CAD, I decided to redesign the system to fit the platform I had. In addition to compatibility improvements, my design featured some improvements to the efficiency of the system through better air flow.
After designing this project, I set out to manufacture it out of aluminum in my high school’s machine shop, despite having no prior machining experience. To my surprise, my shop teacher was on board, as long as I made the parts on the CNC machinery the high school had recently purchased. At the time, there were no instructors who knew how to operate the machinery, so I had to figure it out on my own. After several months of reading any manuals and documentation I could get my hands on, I began to make parts, most of which ended up as scrap.
By the time I finished my outrageously over-ambitious project I had mostly lost interest in air guns, and commercially available designs far outperformed my homebrew designs. While my prototype worked well, the experience I gained from this project was far more valuable than the finished project. During the project I had fallen in love with machining, and I had learned the basics about press fits, slip fits, and O-ring seats. This project set me down the path towards mechanical engineering and is always nice to look back on to see how far I have come from those early days of CAD in high school.