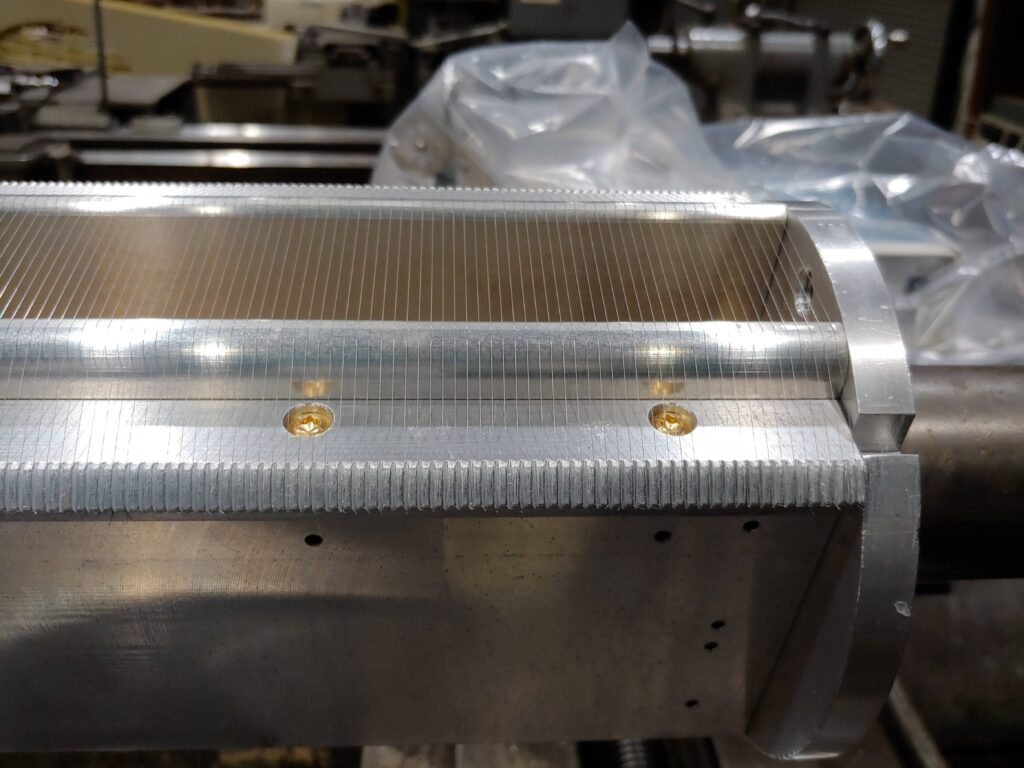
Electrostatic septa are particle accelerator beamline devices that use an electric field generated by a high voltage cathode to steer protons from one beamline into another. To stop the electric field from influencing the path of protons that aren’t meant to be steered, a plane of .004″ diameter tungsten-rhenium wires stretches from one rail of the septum frame to the other. This row of wires creates a wall that electric fields struggle to leak past. Some of the particle beam ends up on either side of the wire plane, and some particles even crash into the wires. This bombardment of particles can cause some of the wires to weaken and break over time, reducing septum performance and causing increased radiation.
The MI-52 septa were designed dozens of years ago using an unusual automated wire installation process. When I started at Fermilab, it had been over a decade since anyone had successfully re-manufactured a damaged septa frame with fresh wires. Anyone who remembered how the process had been done had long since retired, and precious few instructions were left behind. The septa frames themselves are twelve feet long, and almost a half-mile of tungsten-rhenium wire is required to wrap one frame.
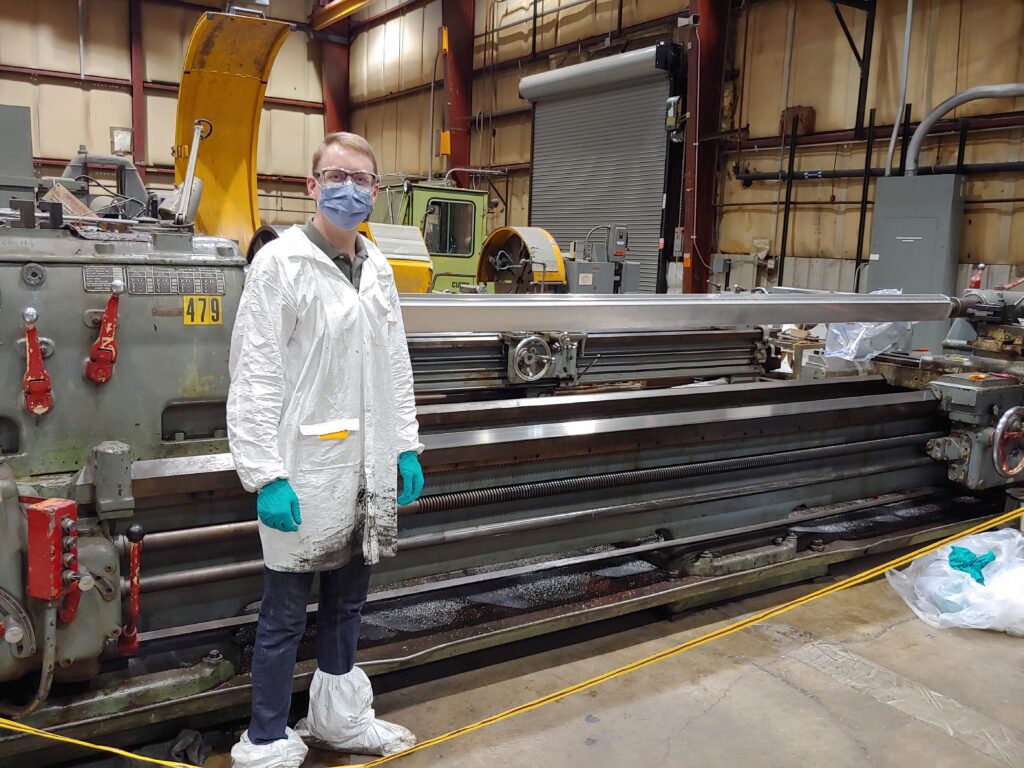
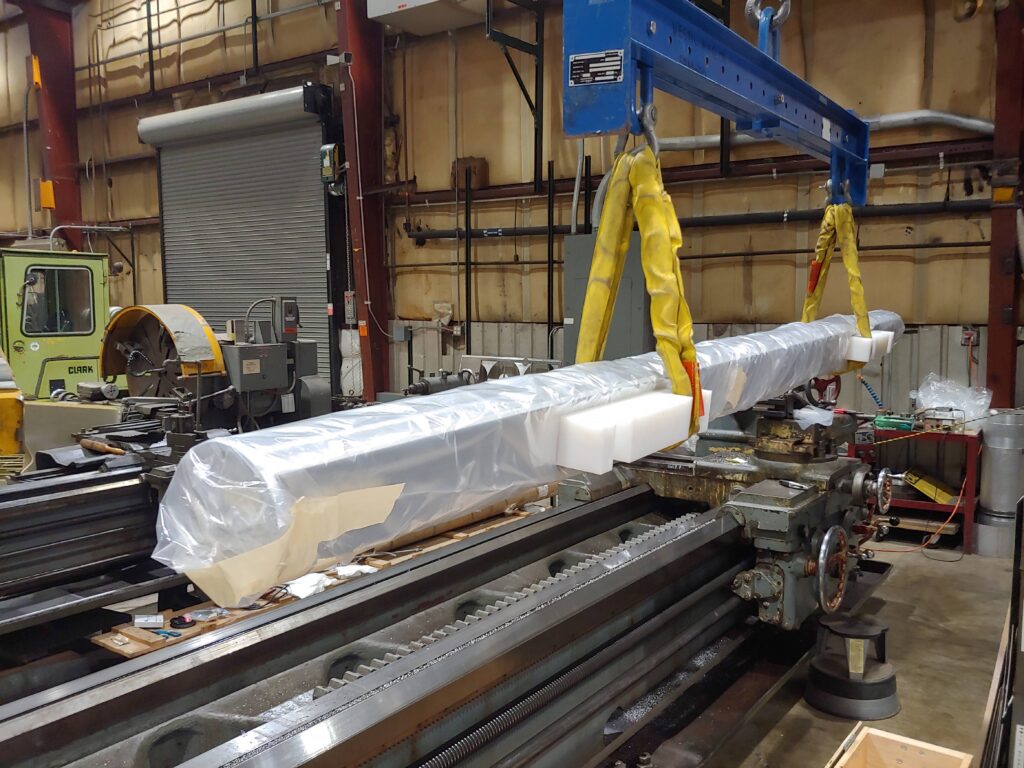
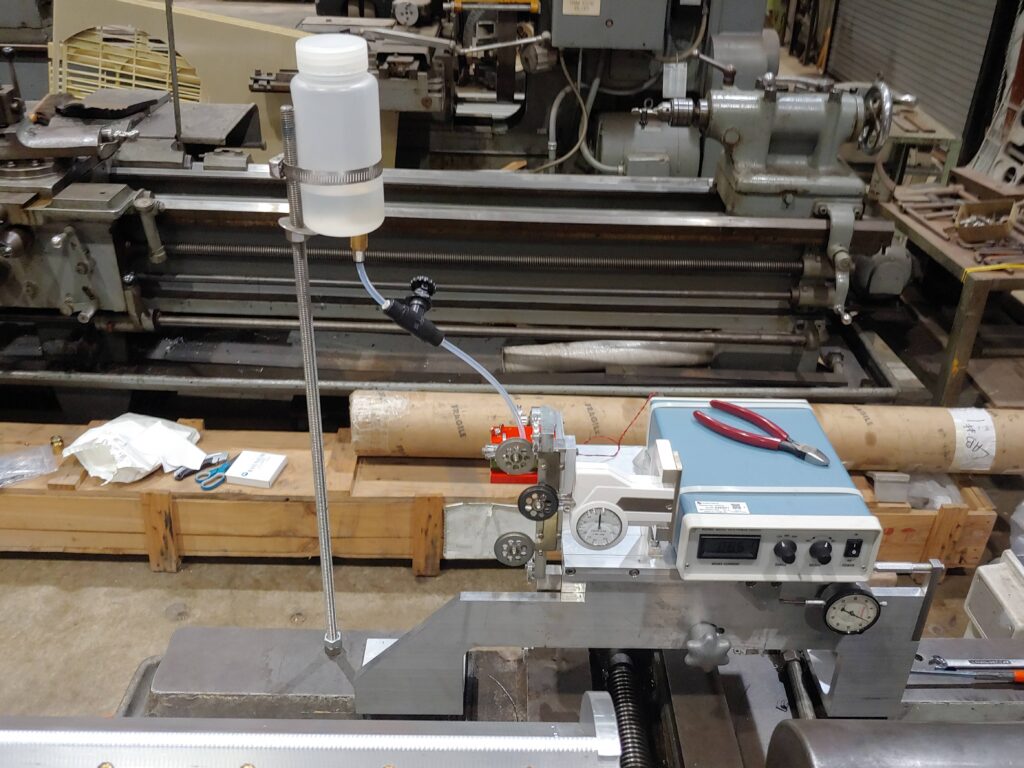
After careful study of the drawings and several tedious weeks in the machine shop, I was able to rebuild the required tooling and successfully re-wind a damaged septa frame on the first attempt with the help of some very skilled Fermilab machinists. The tooling first puts grooves into annealed aluminum bars bolted onto the frame. Wire is then laid in the grooves while tension is precisely set with a variable force electromagnetic brake and tension meter. The same grooving tool is then used to create another set of grooves, offset slightly from the first groove only a few grooves behind where the wire is being laid. The second groove pushes the softened aluminum over onto the wire, locking it into place. The excess wire wrapped around the back of the device is then snipped off, and the frame is ready to leave the shop.