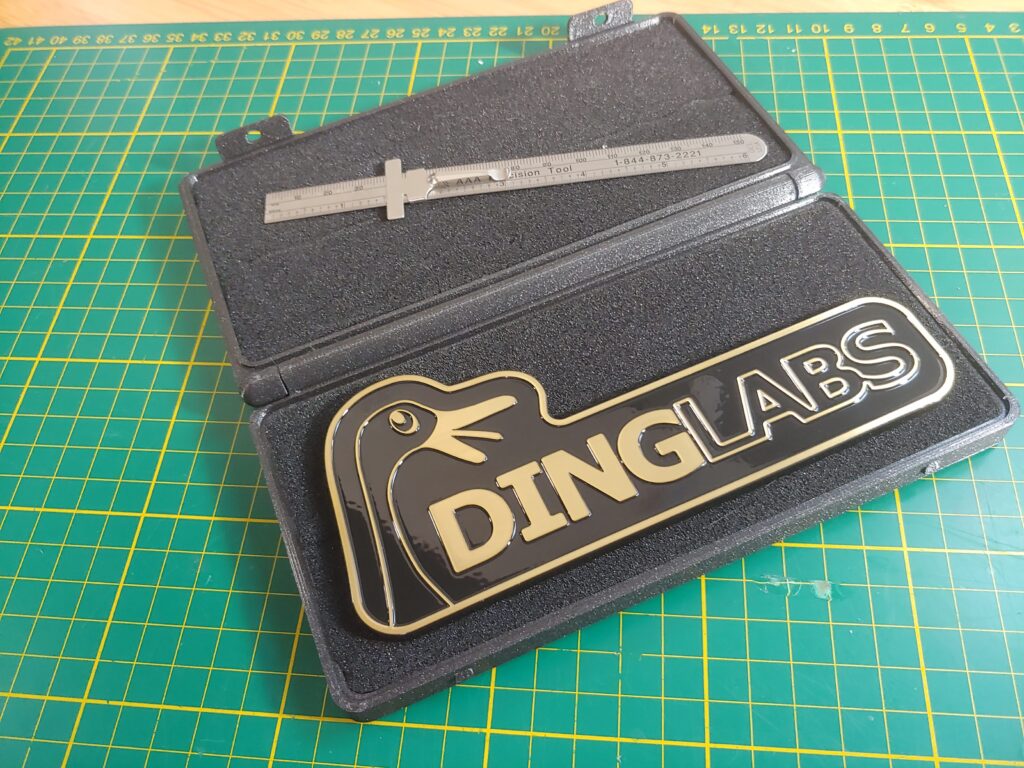
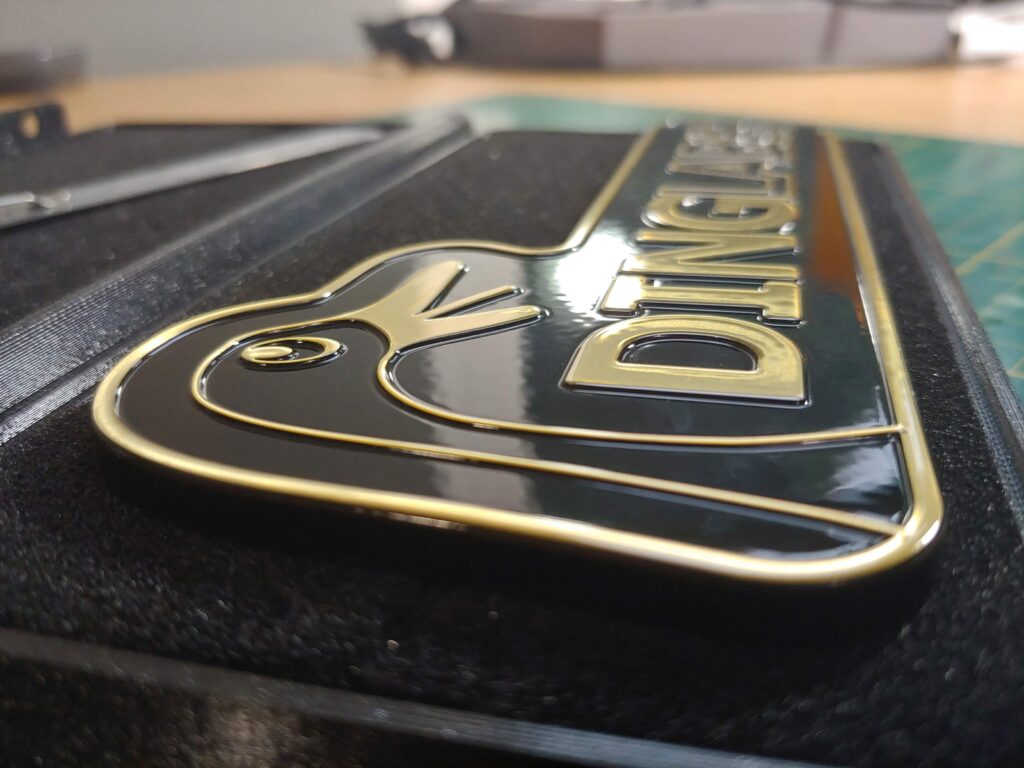
After seeing some great examples of DIY brass nameplates online, I wanted to take a crack at making one to justify the purchase of a powder coating setup if nothing else. I decided to make a spoof of the Thorlabs logo as a housewarming gift for a friend with enough detail to make the machining a bit tricky.
The negative of the design was roughed .05″ deep with a 1/32″ diameter endmill. Finishing was done with a .005″ ball engraving mill with a 20° taper from lakeshore carbide. The finishing with the tapered engraving bit was done with a 3D roughing path in Fusion 360 that allowed the tool to cut further into tight corners on higher Z level passes, then back out on lower passes. That strategy added considerable machining time, but allowed for great detail even with a relatively deep engraving depth. For fixturing I used powder coat masking tape on the aluminum fixture plate and the brass stock with super glue in between.
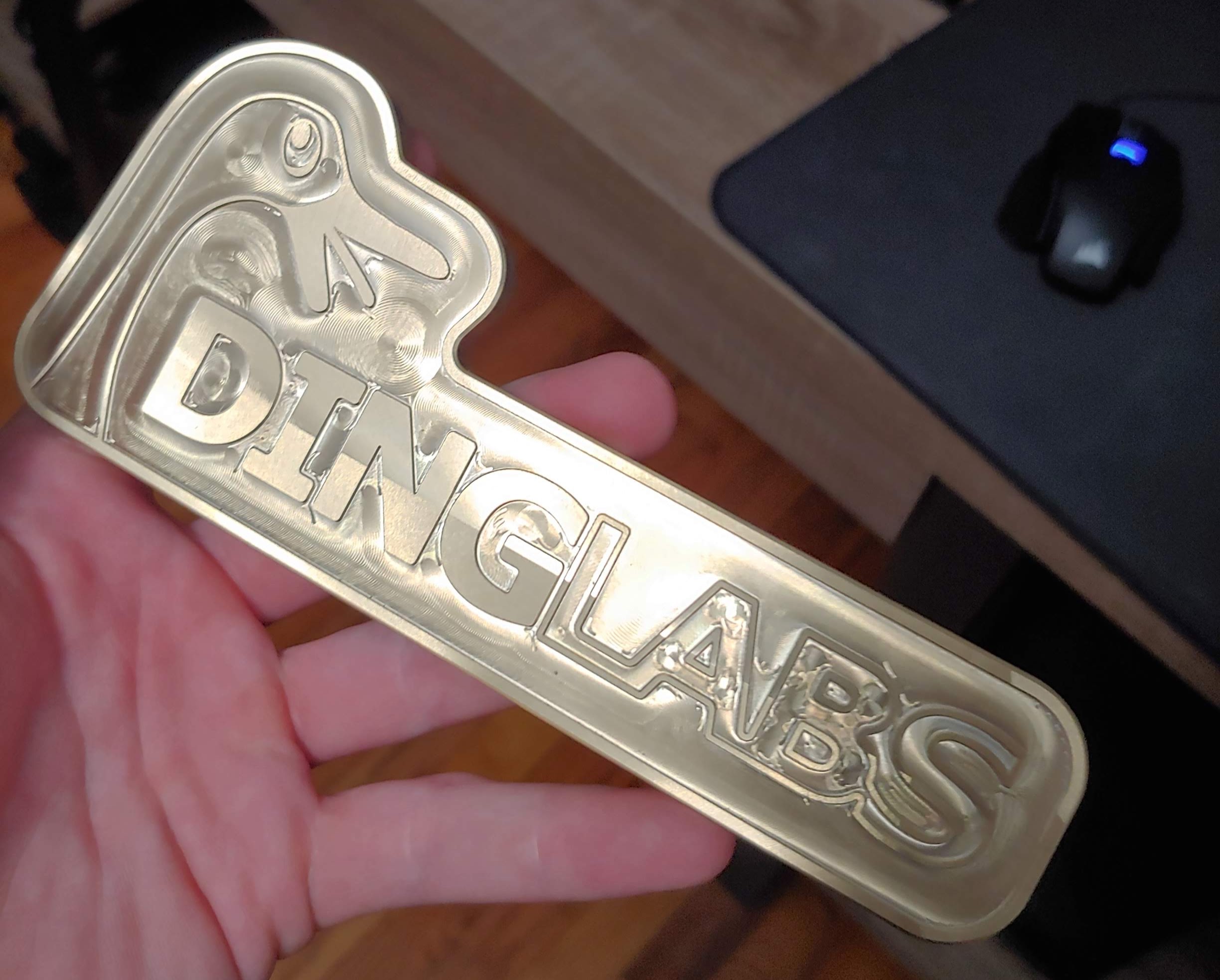
On the backside I milled some pockets to allow magnets to be glued in place after the powder coating was done. At the end I realized I really could have used one more magnet! After machining the part warped slightly, and if all the magnets don’t make contact the plate can slide down the fridge a bit.
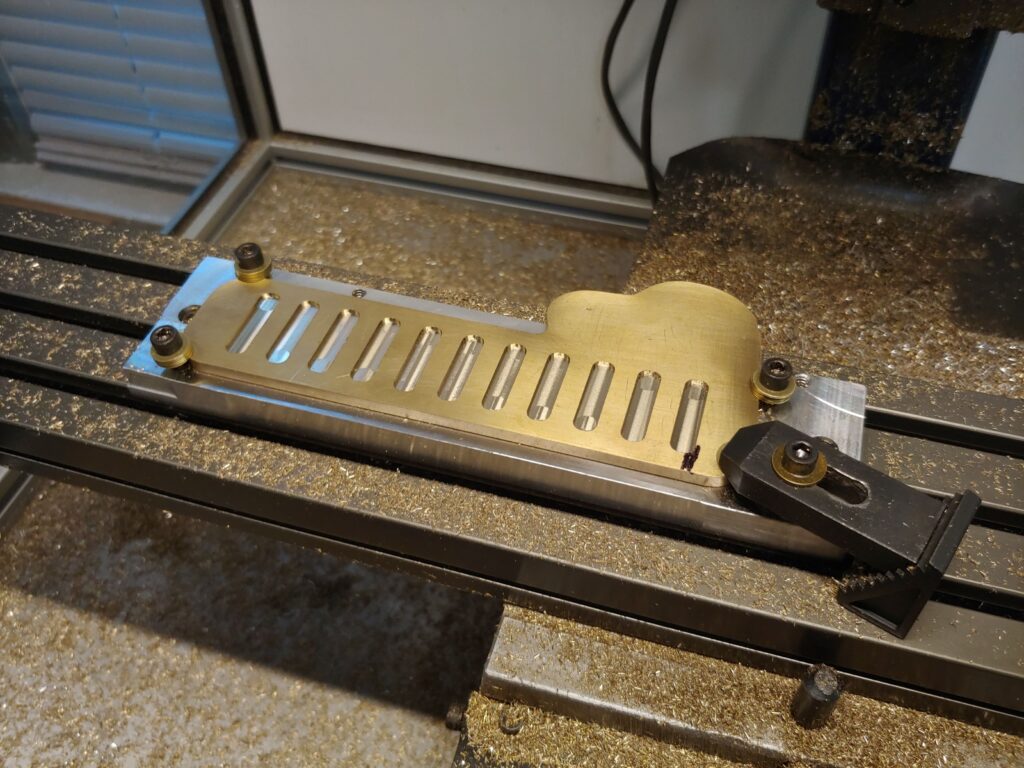
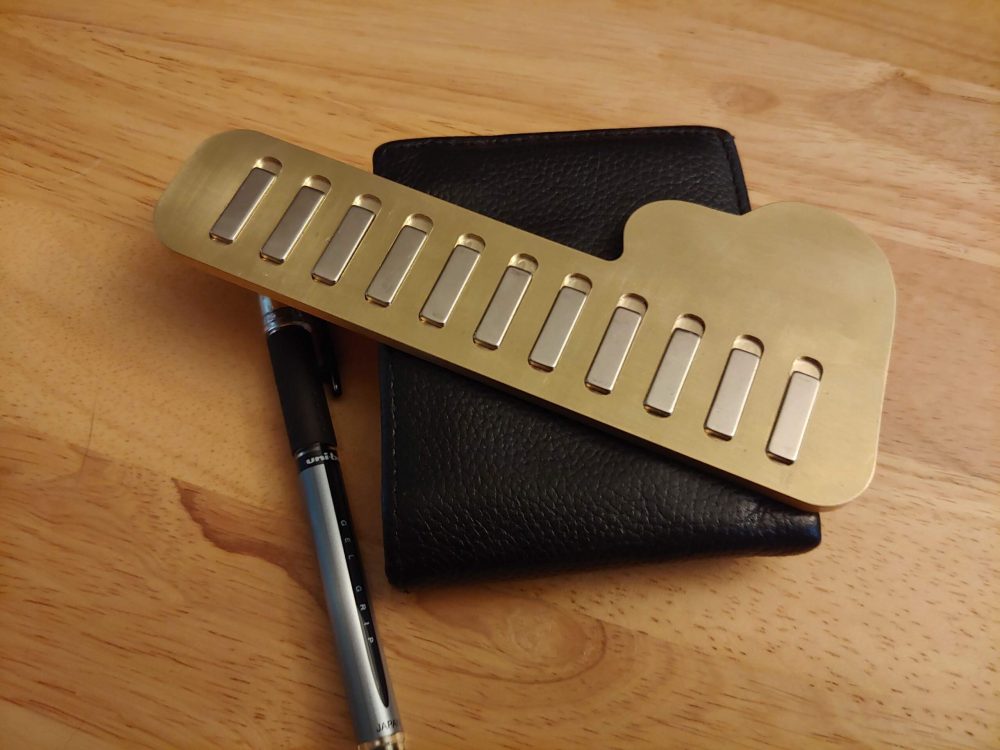
After the machining I powder coated the entire part gloss black and wet sanded the raised areas of the design with up to 2000 grit sandpaper to get a mirror finish. The black powder always goes on easy and looks great afterwards!
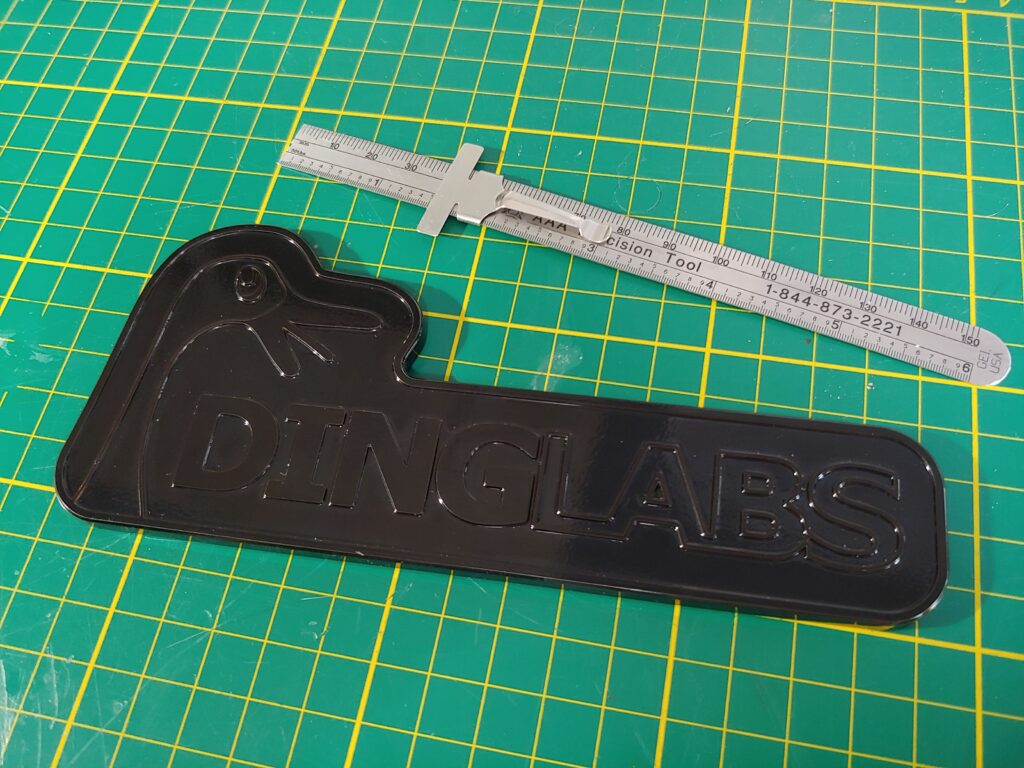
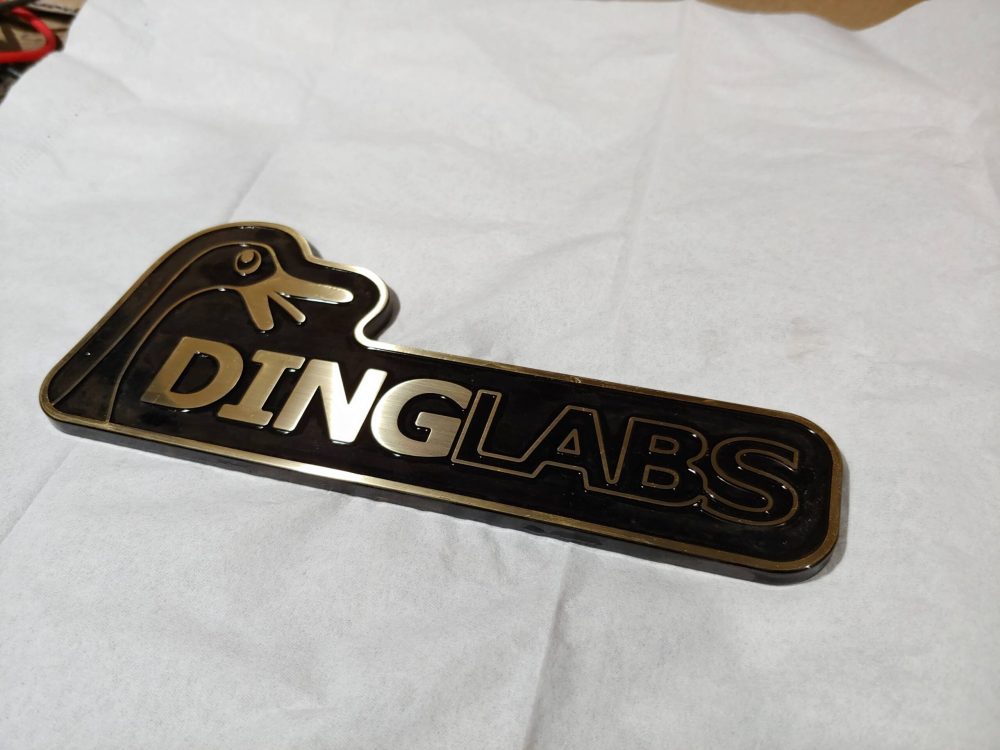
After the sanding the plan was to put on a coat of full gloss clear powder to protect the bare brass surfaces. I found the clear powder to be much more difficult to work with and ended up trashing the first couple parts I tried. After a week of evenings fiddling with settings and prep, the coated parts I pulled out of my toaster oven came out nearly flawless!
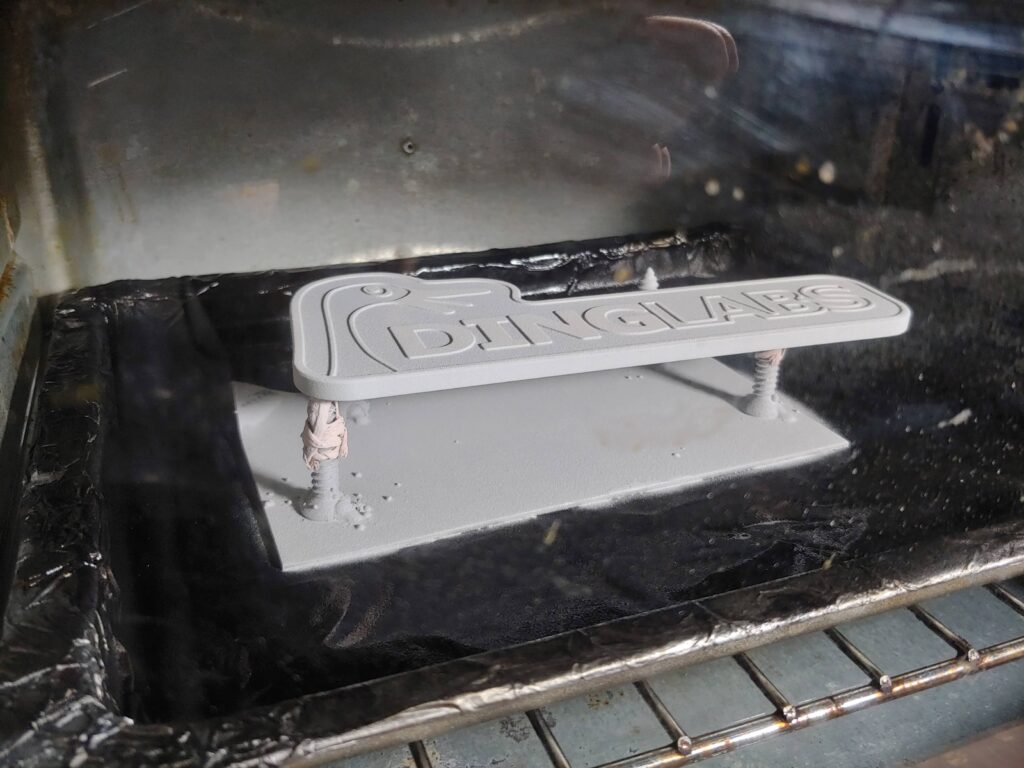
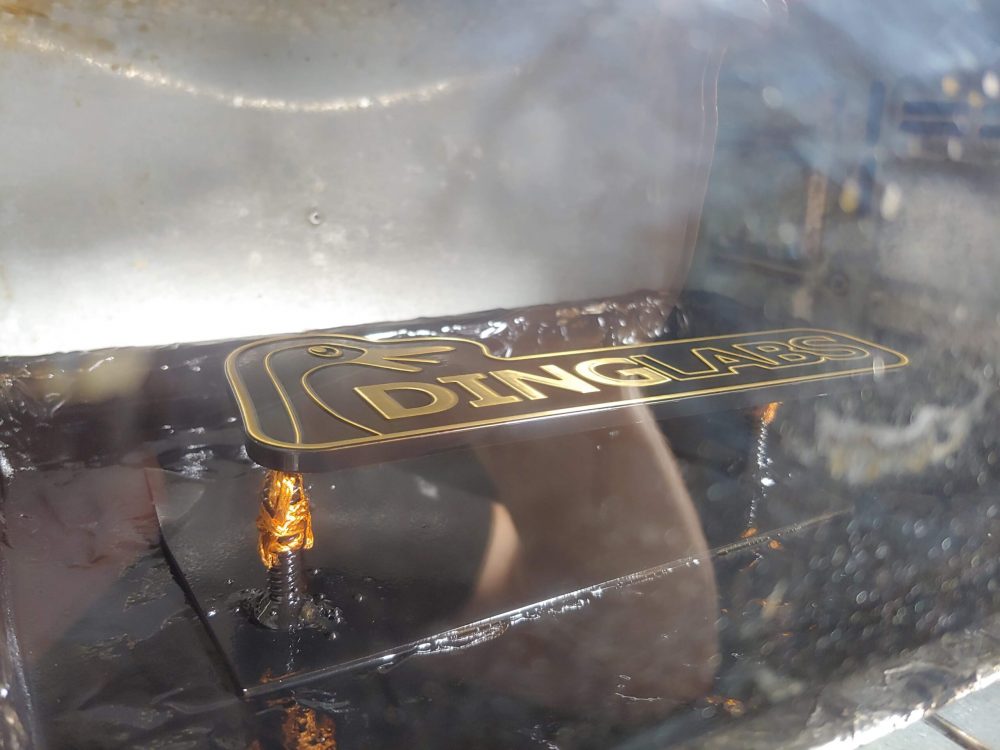
After one scrapped part due to fixture failure, a box of used up sandpaper, and half a dozen powder coating test coupons I was thrilled that the final part came out so well. A few small scratches are forever entombed on the brass behind the clear powder coat despite my best intentions, but almost invisible to all but the most keen observers. Fortunately they don’t show up in pictures! Once the magnets were epoxied in I packaged the nameplate up in its own specially designed 3D printed box and sent it on its way.
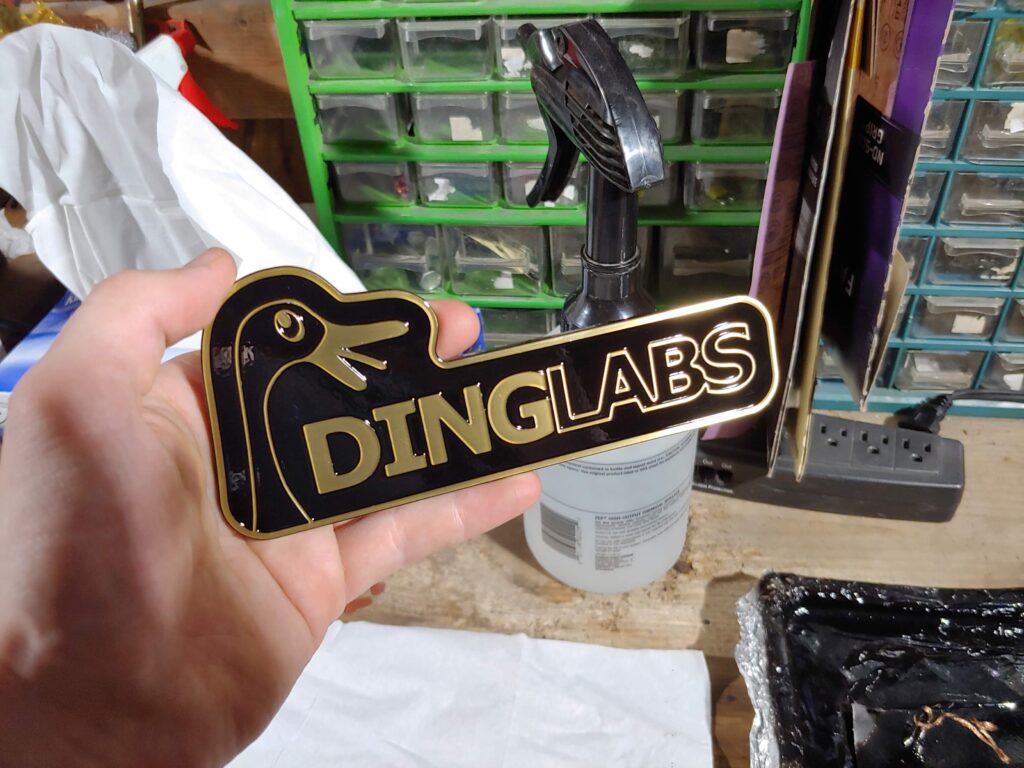