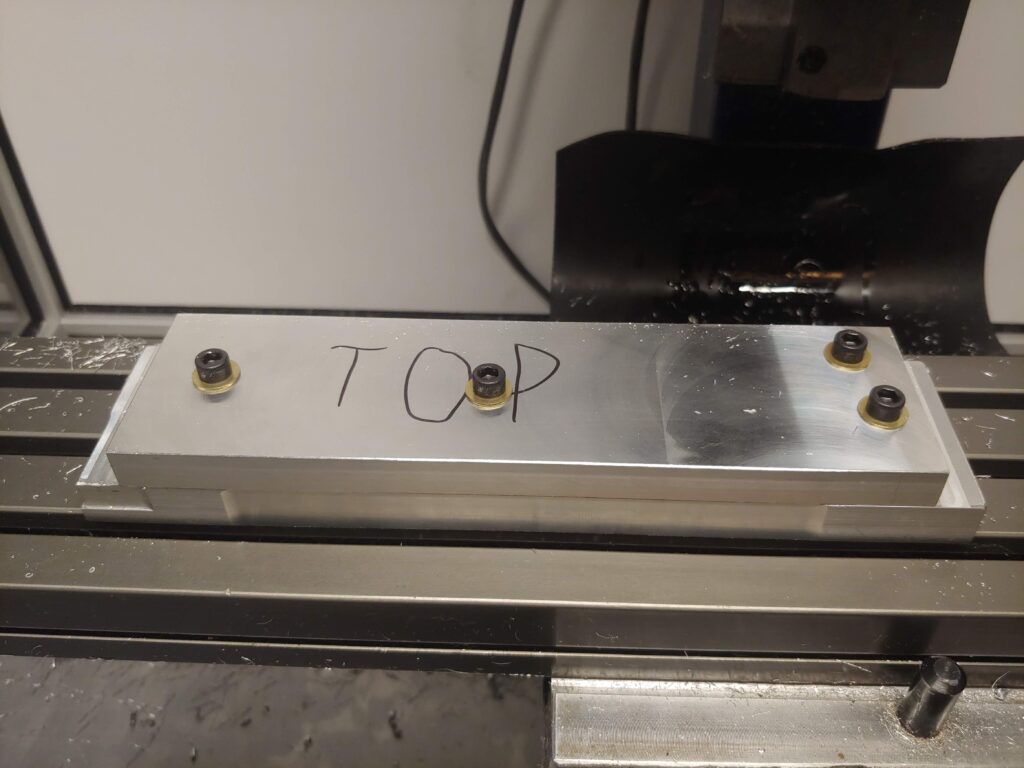
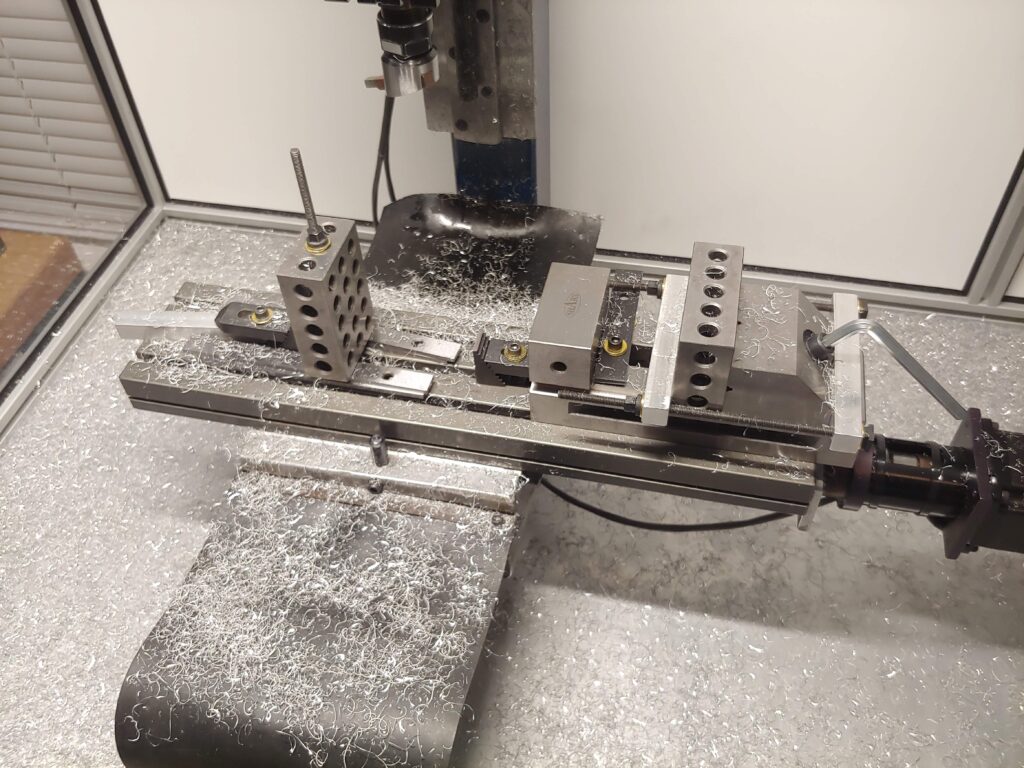
Changing tools in my little Taig mill requires two one-inch open-end wrenches. The mill usually comes with two sheet metal wrenches made from 1/8″ thick material designed to dig into your hands and prevent you from over-tightening your collets by sheer discomfort. Because I bought the mill used, I never had the pleasure of using those wrenches. Instead I have been using two full-sized, forged-steel wrenches. For this application those wrenches are heavy, clumsy, and provide way too much leverage. Because of their weight they can easily chip or break tools if you get careless and bump them into a carbide endmill.
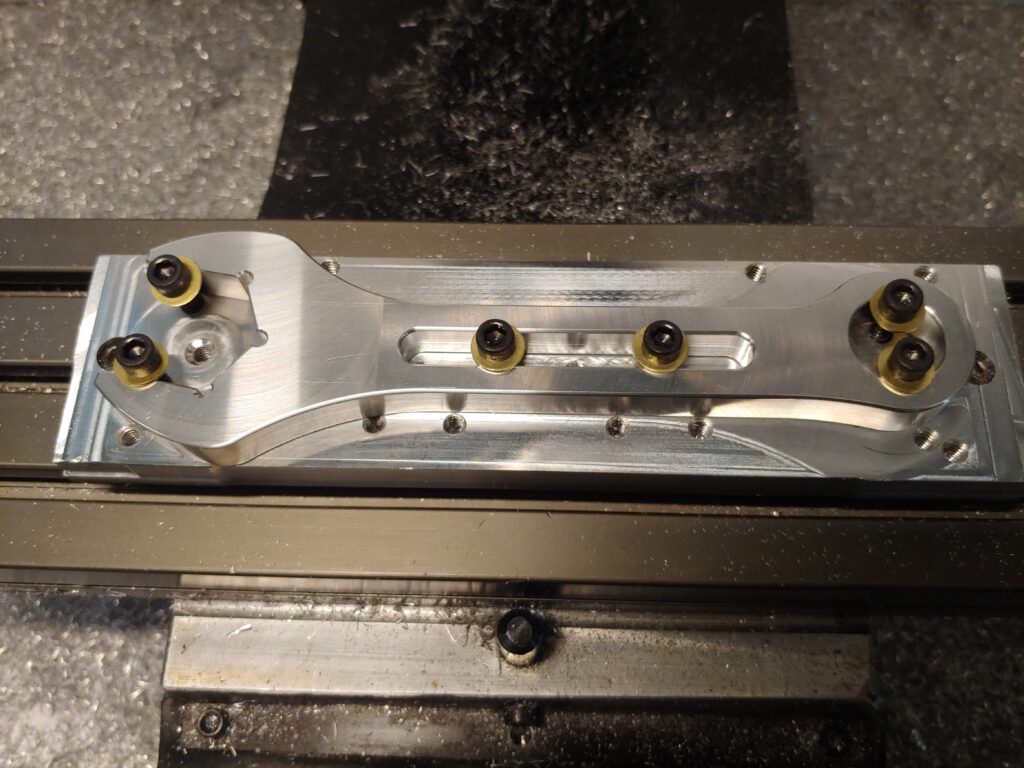
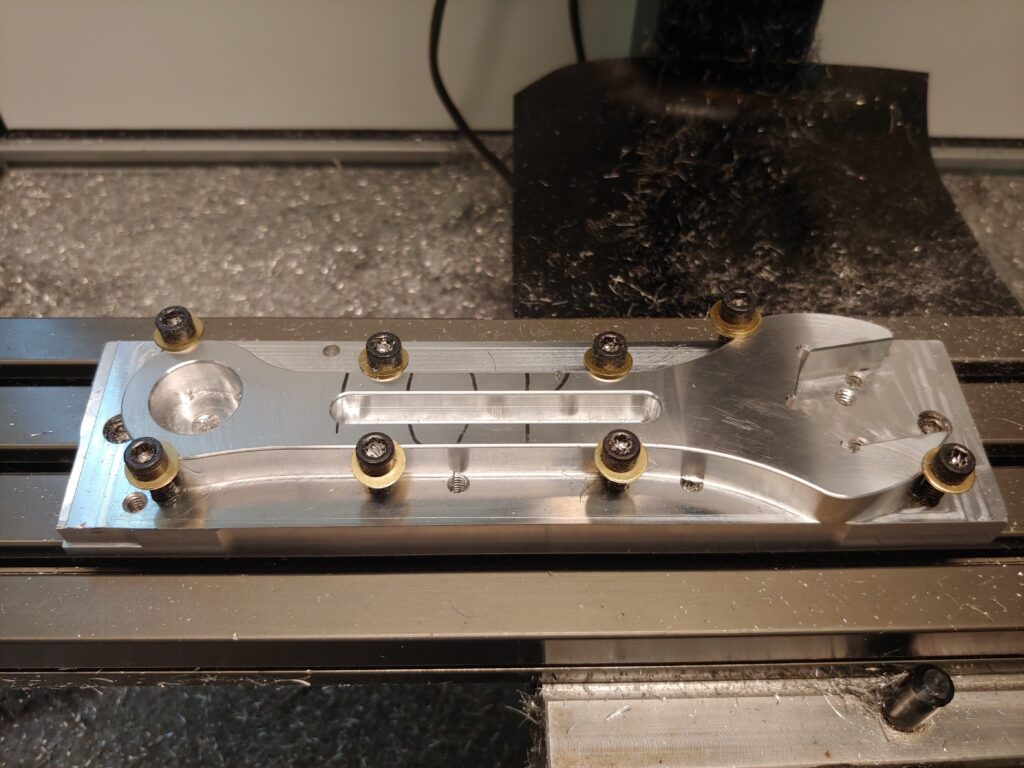
The simple solution would have been to cut the steel wrenches down to have a nice short handle. I decided wanted something a little lighter and more elegant and set out to design some aluminum wrenches. In addition to being lighter and properly sized, aluminum wrenches won’t damage the already damaged finish on my collet nuts. It’s also much harder to damage an endmill from a slight bump with a lighter, softer tool. I decided on a 7″ long wrench with a slightly offset eye for hanging it on a rack. The offset eye allows the wrench to hang straighter on a tool rack since some of the mass is shifted off-center by the tilt of the wrench end, but admittedly the eye is offset more than necessary just for looks. A 7″ piece of stock is just big enough to make facing in one pass require all sorts of fixturing gymnastics, because we wouldn’t want a project that was too easy! See the picture on the top right for my improvised table vise.
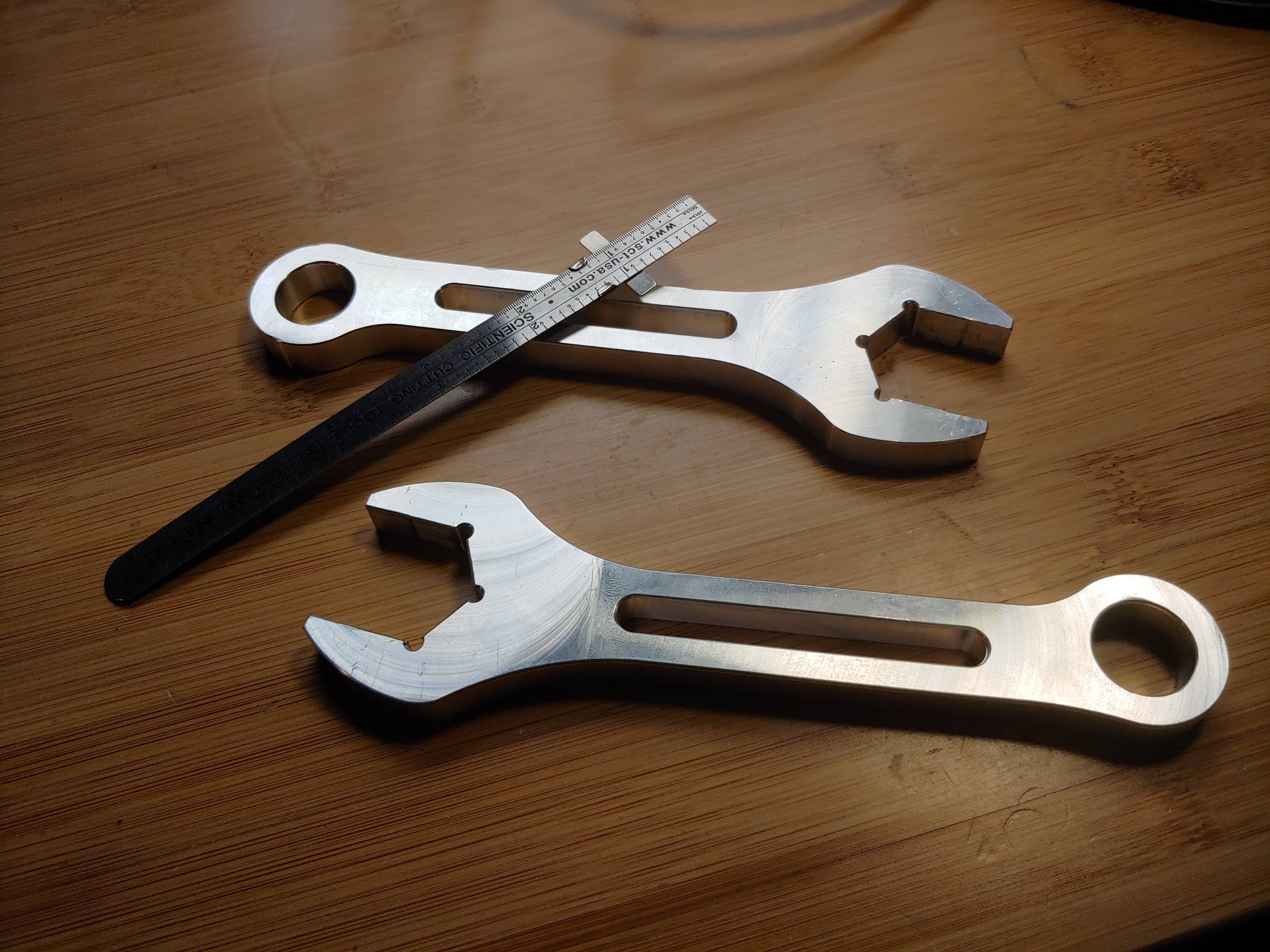
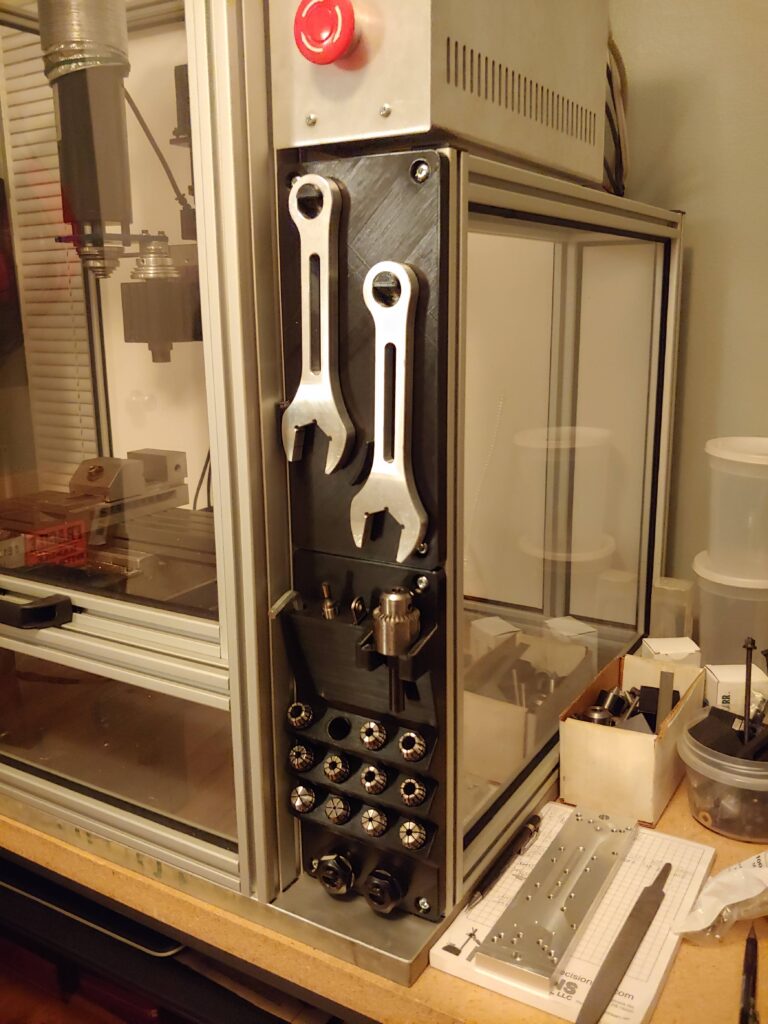
I designed a single knife-maker’s style fixture using brass washers and cantilevered screws to clamp the parts for each of the four machining operations. In total it took a couple dozen fixturing holes just to make a couple little wrenches! To add a nice finished look to the wrenches I used a corner rounder to add a .050″ radius to all the edges, except those inside the wrench throat. Those all received a .030″ machined chamfer, since the radius tool couldn’t squeeze into the tight contours around the drilled out corners. If I had the equipment I would love to bead blast and anodize each wrench, but shop-made tools rarely receive the finish they deserve. For now I’m happy not having to lug the forged steel wrenches from underneath the bench at every tool change.