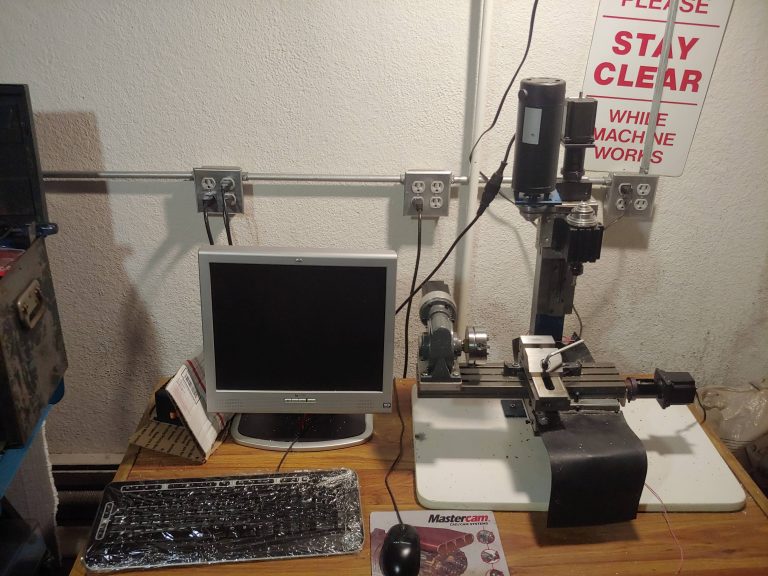
My interest in CNC machining began back in high school, but the time that CNC machine tools were available to me was limited to a few hours a day when the teacher was in or around the machine shop. The high school had a small benchtop CNC mill in the corner that at the time was about 12 years old and had not been used in a decade. I offered the school $200 for the machine, and they were happy to have it gone. I was thrilled to finally have all-hours access to a CNC machine, but getting the mill up and running was a much larger project than I had anticipated.
I purchased the machine not knowing anything about it other than that it was once used to machine wax for small investment casting projects. The mill was covered in wax chips from ten years ago and had no manuals or information about its operation. After some searching, I discovered the mill was a Taig benchtop mill that had been outfitted with custom electronics by a small company that sold the mills to schools as part of a turn-key casting project for making jewelry. I was even able to contact the engineer who originally outfitted the mills with the electronics who told me the mill ran on a proprietary MS-DOS program.
I decided the best thing to do would be to retrofit the mill with new stepper motors and a modern windows-based CNC machine control software called Mach 3. I disassembled the entire mill for cleaning and found several parts worn and broken. Fortunately, Taig still makes the same mill today, and I was able to purchase the necessary parts to repair and upgrade the machine for CNC operation. I reassembled the mill according to Taig’s posted factory procedures and built a control box around the then popular Gecko G540 4-axis servo drive. I installed and wired new stepper motors and had my own fully functional CNC mill. Once I began college and had access to a CNC machining center at NDSU, the machine sat idle most of the time, but prior to that the machine got quite a bit of use. I made several prototype parts on it and did a few small production jobs like the mic adapters shown in the picture. I hope to get back to using it once I finish college with a bigger budget for tooling than I had in high school.
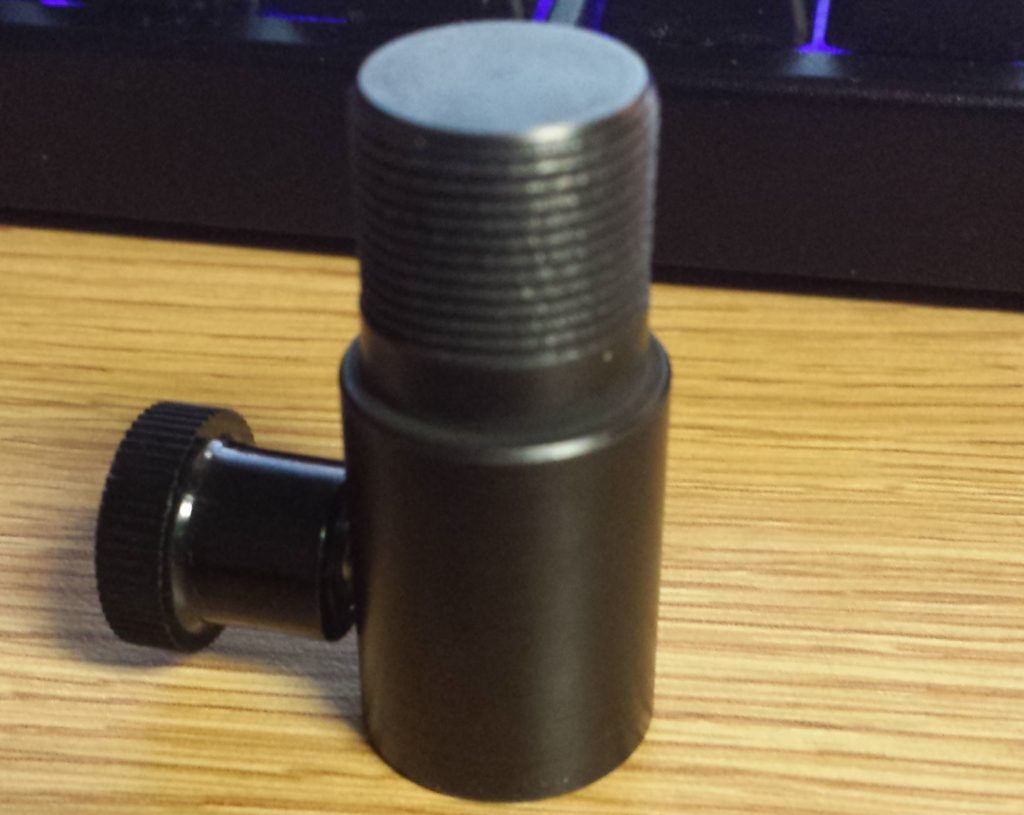