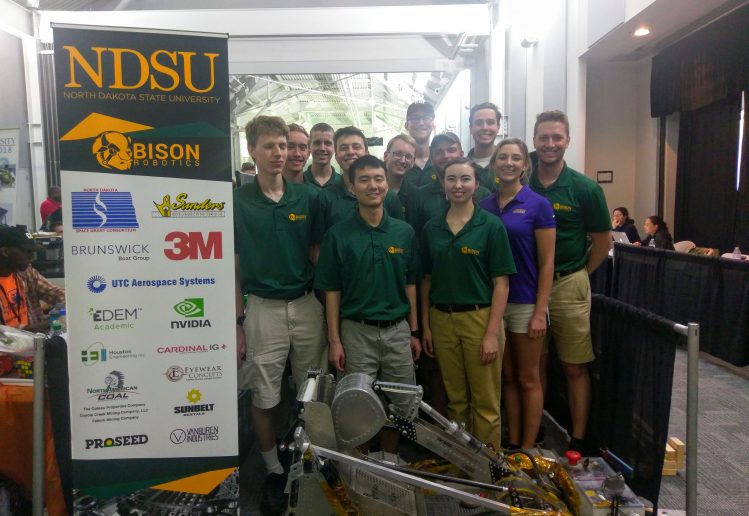
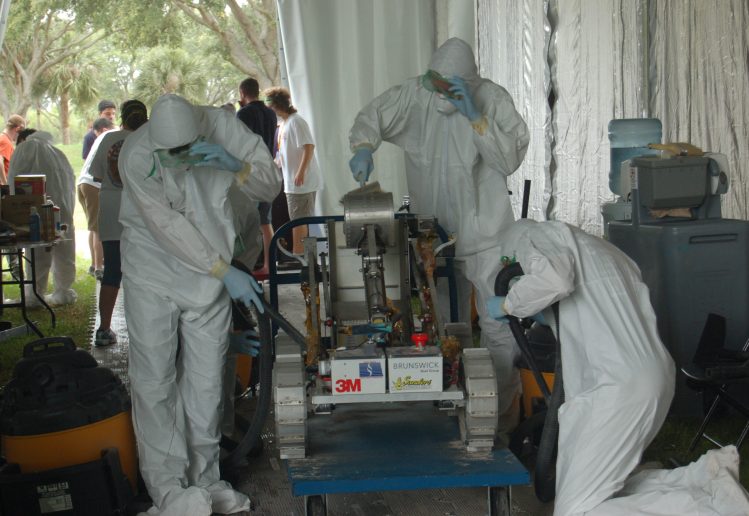
After an exciting 2017 competition year with the NASA Robotic Mining Competition, I decided I wanted to be as involved with the project as possible and put in a bid for the position of project lead. When I became the project lead, I focused on improving the project’s organization on the mechanical side. Through the implementation of a new CAD program, PDM software, a master BOM, and scheduled design reviews, the project team was able to design and build a much more complex robot than the previous year in a much shorter time frame. I also focused on bolstering our team’s performance in the outreach, slide presentation, and systems engineering paper categories of the project. At the 2018 NASA Robotic Mining Competition the NDSU team took home 2nd place overall out of 44 teams, the Innovation Award, 1st place Slide Presentation, 2nd Place in On-site mining, and 2nd place in autonomy.
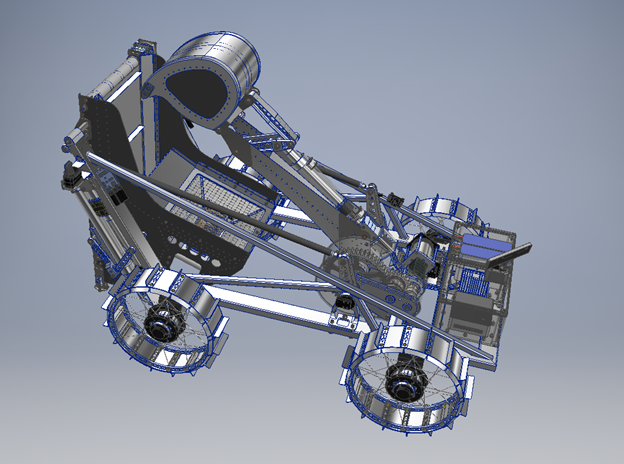
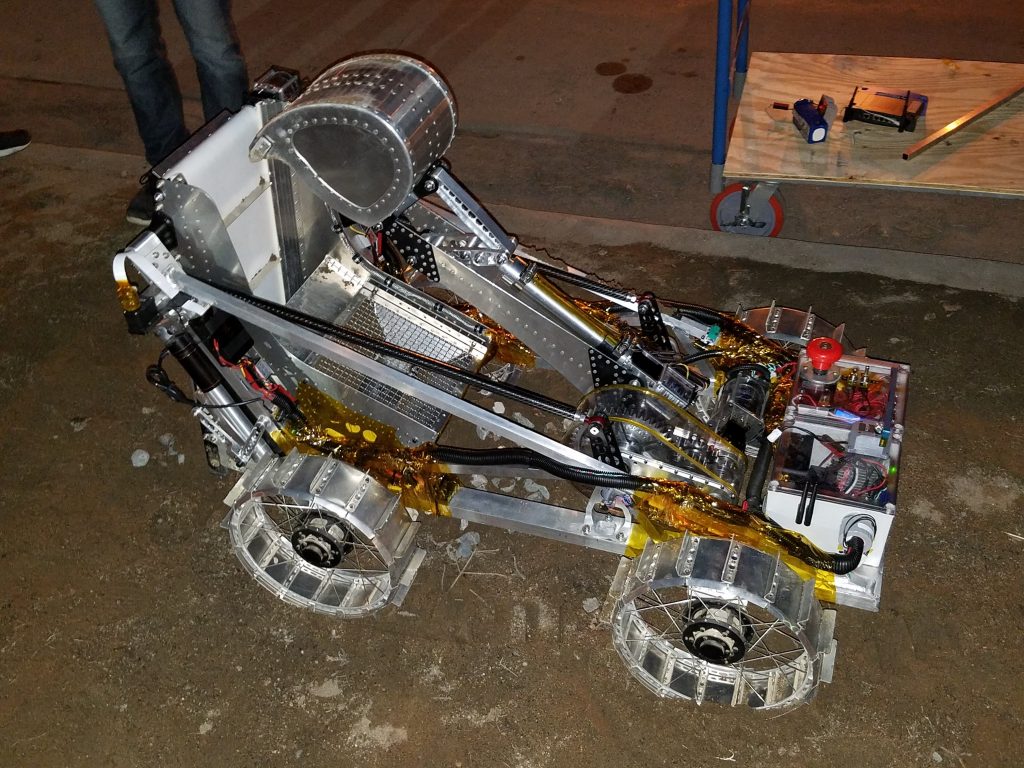
In addition to my responsibilities as project lead, I developed and designed several robot systems. One of my contributions to the robot was the design of a unique set of spoked wheels. Because of the robot’s skid steer control scheme, turning generates large side loads on the wheels that caused previous wheel designs to deflect or fail. The spoked wheels are extremely light at 3.1-lb each but are capable of withstanding side loads greater than 150-lb with minimal deflection. To ensure the design was feasible before the final wheel design was completed, I wrote a Matlab program that found the tension of each spoke based on any given loading conditions. By inputting our estimated loading conditions when turning, I was able to calculate the minimum necessary tension of each spoke, and verify the necessary tensions were reasonable.
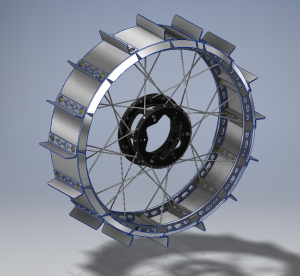
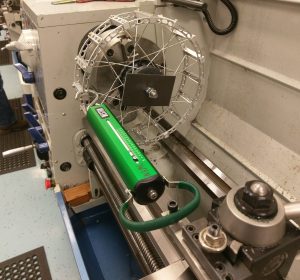
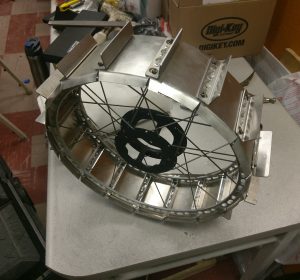
Our robot also featured a unique drivetrain and a custom linear actuator. Another member of the project completed the initial design for both systems and I modified each system for increased load carrying capacity, functionality, and manufacturability. In the case of the linear actuator, I worked with the original system designer to select a more appropriate bearing configuration for the types of loading involved. I also modified the coupling between the linear actuator lead screw and the motor to allow the coupling to handle 150% more torque. To allow the limit switch positions on the actuator to be adjustable, I designed a simple and flexible mounting solution for our custom limit switch circuit boards. This improved the reliability of the limit switches significantly and helped prevent the system from crashing into its end stops.
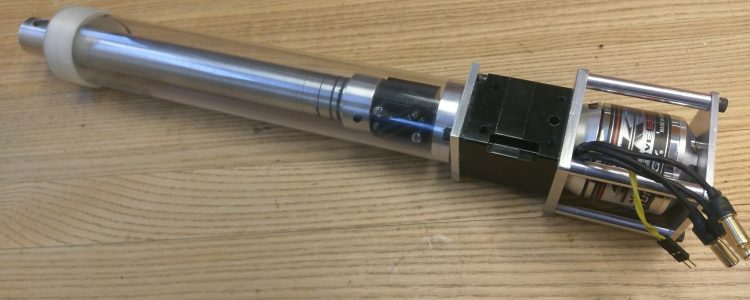
During my work on the robot drivetrain I refined the conceptual design into a functional system with bearings appropriate for the loads and simplified the overall design. I also modified several features of the drivetrain for easier assembly and manufacturing to save time and improve the precision of the drivetrain. After prototyping and testing the system, some changes were made to the bearing configuration, as well as the sealing mechanisms, to allow for a reliable and rigid drivetrain unit. In final testing, the unit which weighed 4-lb was capable of outputting 75 ft-lb of torque before failure.
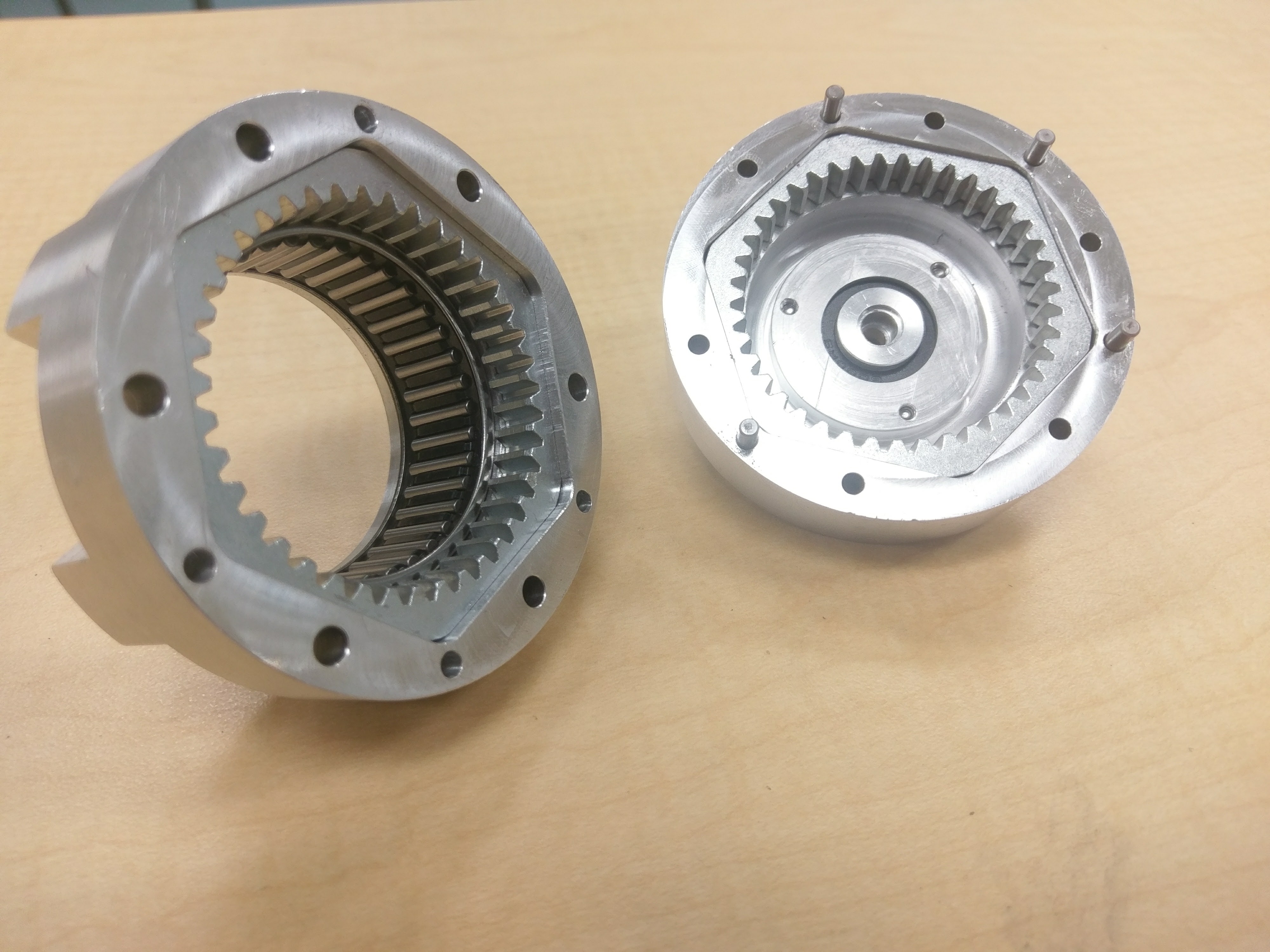
In addition to all the design tasks I carried out on the robot, large and small, I was extremely proud that our team did the entirety of the machining for the robot in house. I machined every CNC milled component on NDSU’s Fryer CM-15 machining center, and many other components were machined manually by myself and other team members. We outsourced most of the sheet metal work due to lack of equipment, and some of the aluminum welding because of the associated difficulty, but most of the robot was built in the Manufacturing and Industrial Engineering machine shop by NDSU students.