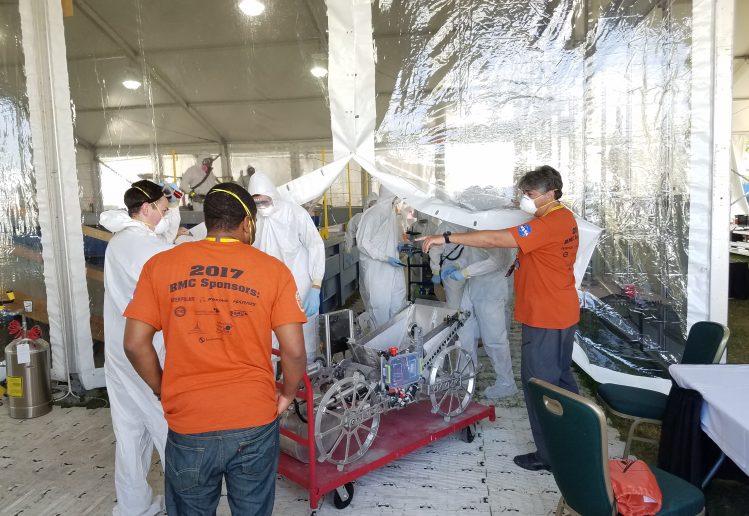
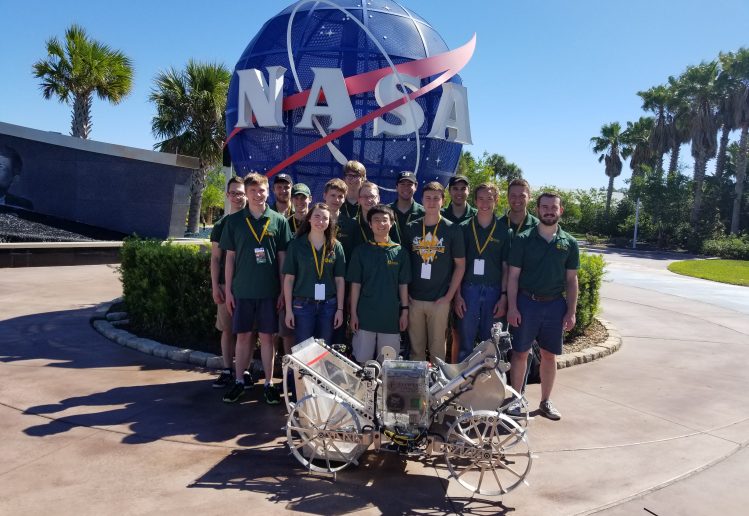
Unfortunately, no high schools in my hometown of Fargo North Dakota had a robotics program during the time I attended. When I arrived at college, I never thought to seek out a robotics club, but upon discovering Bison Robotics I found the projects available were the perfect fit for my set of skills. More importantly, the team working on the NASA Robotic Mining Competition project were all exceptionally excited, motivated people. When I first joined the club, I acted as a manufacturing lead and consultant but quickly began helping with the design of the robot. At the 2017 NASA Robotic Mining Competition we placed 4th out of 47 teams in the On-site mining category, and 11th overall.
When I met the team for the NASA Robotic Competition, they had begun working on a new robot for their second year of competition. With an almost entirely new team from the previous year it was a completely blank slate. In previous years, the team built most of the robot with 2-in x 1-in rectangular aluminum tubing, crudely jig-sawed sheet metal, and off-the-shelf components that were not well suited to the application. I introduced the mechanical team to the NDSU Industrial and Manufacturing machine shop manager and began teaching all the team members how to use manual mills and lathes. Within a few months, we redesigned the robot to take advantage of custom components that could be made with precision several orders of magnitude greater than the previous competition year.
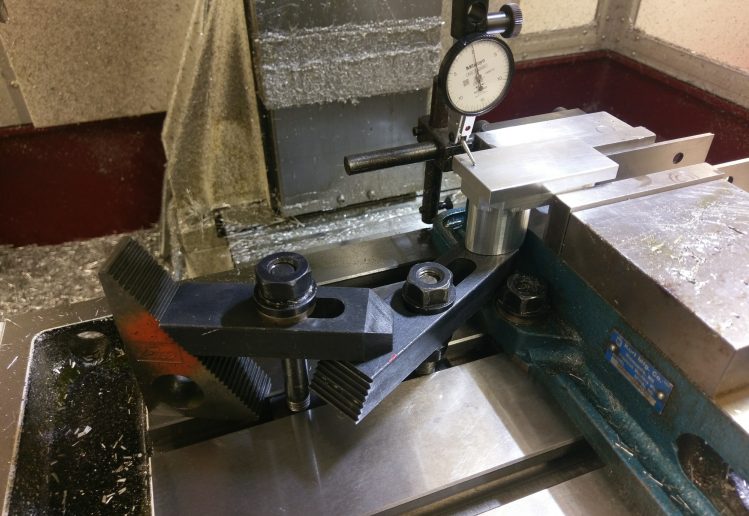
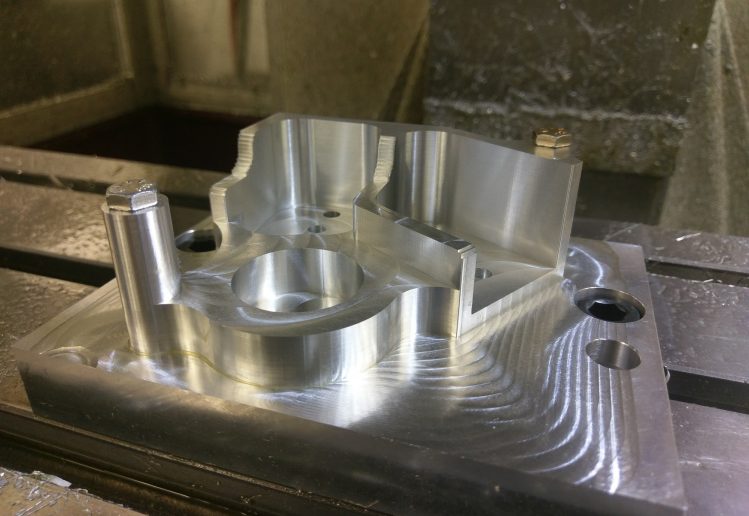
While continuing to manufacture many components of the robot, I also redesigned the robot’s deposition bucket which used a winch to rotate the bucket nearly 180 degrees and dump its contents. The digging and deposition systems were initially designed to be as large as possible, so they could mine and deliver the most mining material. However, as these systems were integrated into the overall robot design, it was found that they left very little space for the drive systems that powered them. To make matters worse, the suspension system we had incorporated into the H-frame of the robot left very little space to mount the drive systems. After many hours of brainstorming with another engineering student, we came up with several complex, but compact drive systems that could drive our digging and deposition systems.
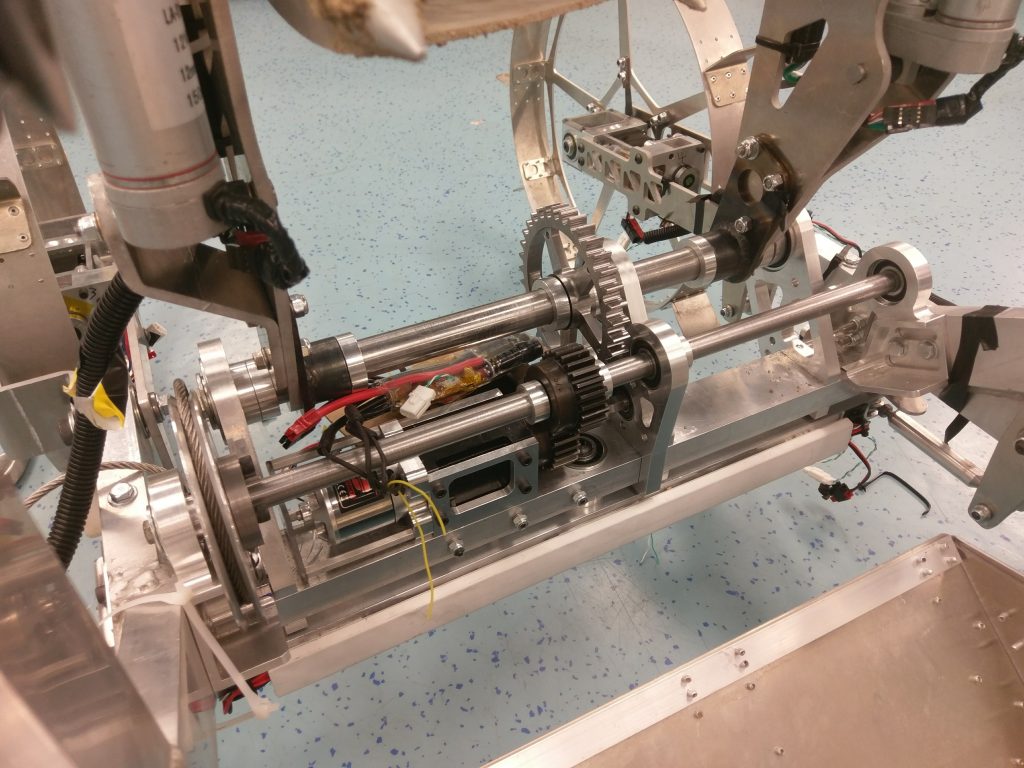
I also worked on the wheel and drivetrain assemblies of the robot to keep them as compact as possible. Once again, the digging system designed independently of the other systems significantly restricted the space available for our drivetrains, so it was decided to tuck the drivetrain inside the wheel hub itself. I suggested a very thin hub welded directly to the drivetrain axle that would solve some of our clearance issues between the wheel and the drivetrain.
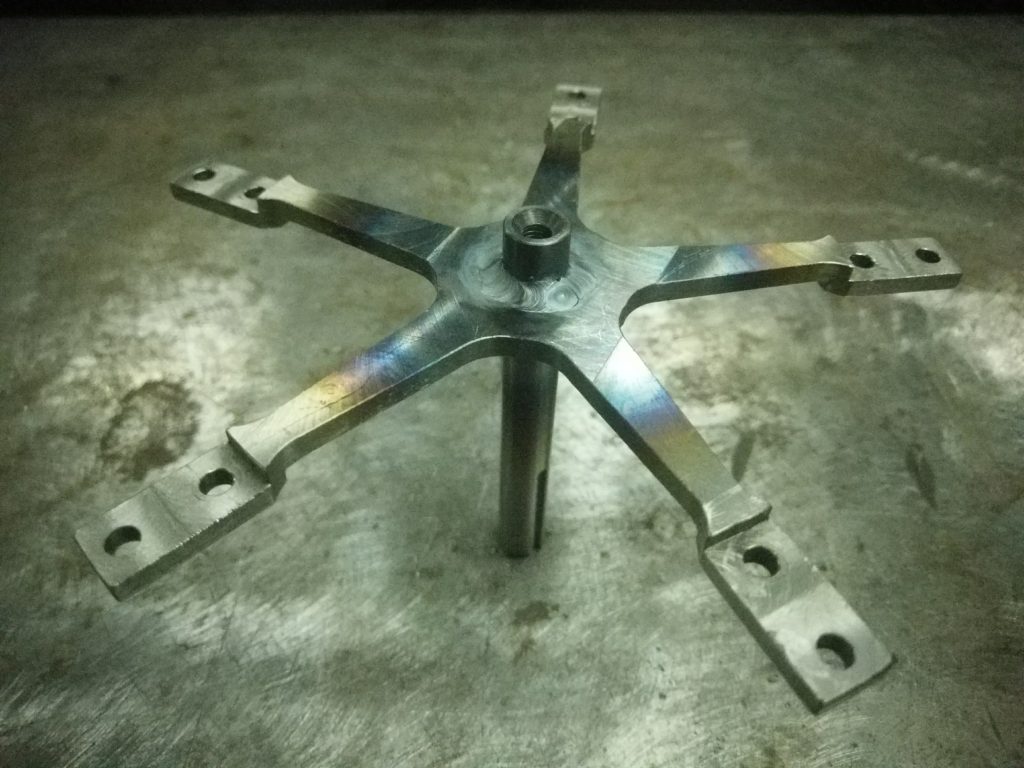
While the team was extremely proud of this drivetrain, it was extremely problematic in practice. The gearboxes we selected failed at a much lower torque than they were rated for, and the wheels themselves were too thin to be rigid enough to allow turning in place. Our clever mechanical suspension provided so much traction that turning with a skid steer control method was almost impossible. Despite these issues, the robot performed very well at the competition and mined a significant amount of material. The lessons I learned were helpful in designing the robot for the 2018 competition year and gave me the experience I needed to design the extremely rigid wheels and drivetrains used on the 2018 NASA Robotic Mining Competition Robot.